Reducing Fit Test and Production Approvals: How AI is Accelerating Production in Small Garment Factories
| Jan, 29 , 25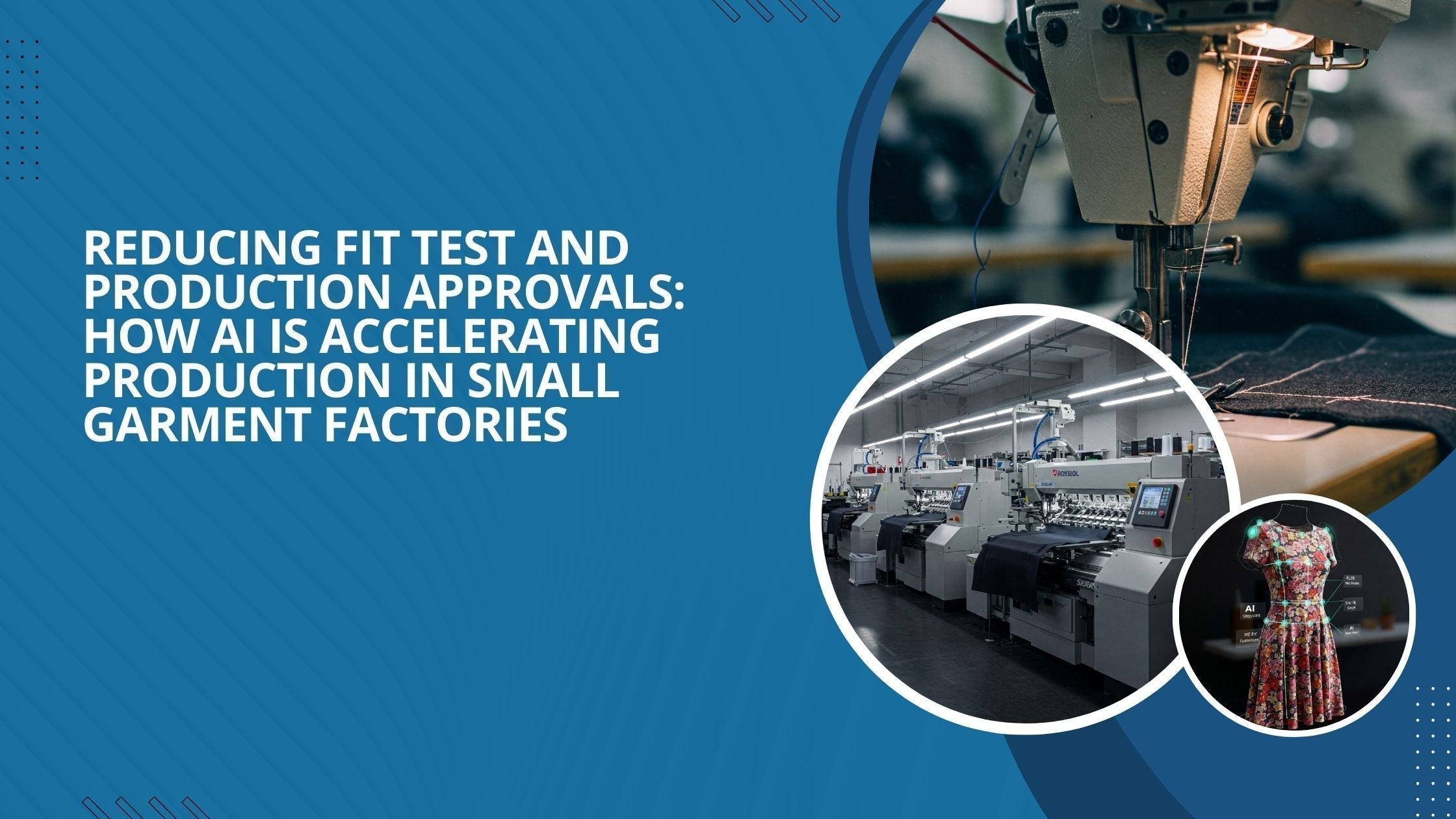
For small garment factories, navigating the complexities of garment production can be particularly challenging. One of the most significant hurdles is creating and approval of pre-production (PP) samples. These samples, made with the same fabric, trims, and accessories, ensure quality and consistency in bulk production. However, the traditional process relies on manual labor and multiple physical iterations, often leading to significant delays, impacting lead times and profitability for small garment factories. This blog examines how AI provides a much-needed solution, streamlining the PP sample process and empowering smaller businesses to compete more effectively.
Understanding the Traditional PP Sample Process and Its Inefficiencies for Small Garment Factories
The journey from design concept to bulk production in a small garment factory hinges on the pre-production (PP) sample. This crucial prototype has the same fabric, trims, and accessories intended for the final product. They serve as the benchmark for quality, fit, and construction. However, the traditional process of creating a PP sample is often fraught with inefficiencies, particularly for smaller factories.
Here's a breakdown of the typical steps involved:
-
Specification Sheet: The process begins with a detailed specification sheet from the buyer, outlining all design specifications, measurements, materials, and construction details. This sheet is the foundation for all subsequent steps.
-
Pattern Making: They create patterns based on the specification sheet. It is still a manual process involving paper, rulers, and other drafting tools in many small garment factories. Significant manual input and expertise are often required even when using CAD software.
-
Proto Sample: A preliminary sample, known as the proto sample, is created using readily available materials. This sample is primarily for initial design evaluation and may not reflect the final product. They send it to the buyer for initial feedback.
-
Trims and Accessories Approval: Once they approve the proto sample, the buyer sends trims and accessories (buttons, zippers, labels, etc.) to the factory for approval.
-
Lab Dip: A lab dip is a small fabric swatch dyed to match the buyer's desired color. They send it for color approval.
-
Fit Sample: A fit sample, made with the final fabric, is created to check the garment's fit and measurements. This sample is crucial for ensuring proper sizing and silhouette. They send it to the buyer for fit evaluation.
-
PP Sample (Pre-Production Sample): After the fit sample is approved, the PP sample is ready. This sample has all the final materials, trims, and accessories and represents the final product going into bulk production. It is submitted to the buyer for final approval before production commences.

The Time and Action (T&A) Calendar:
To manage this complex process, merchandisers typically create a Time and Action (T&A) calendar, a spreadsheet that outlines all key processes and their planned completion dates. This calendar helps track progress and identify potential delays. Key information required for creating a T&A calendar includes:
-
Process flow and tasks: A detailed list of all steps involved in the order, from initial design to shipment.
-
Production capacity: The factory's capacity for cutting, sewing, washing, and finishing.
-
Sewing capacity: We break down the sewing department's capacity by batch and product type.
-
Lead times: The time required for various activities, such as raw material procurement, sampling, and production.
-
Shipment/Ex-factory date: The planned date for the goods to leave the factory.
Crucial dates within the T&A are the Planned Cutting Date (PCD) and the Ex-Factory Date, as delays in earlier stages will directly impact these critical milestones.
Potential for Errors, Rework, and Delays:
Each step in the traditional PP sample creation process is susceptible to errors, which can lead to costly rework and significant delays for small garment factories:
-
Pattern errors: Incorrect measurements or drafting mistakes necessitate pattern revisions.
-
Cutting errors: It results in mismatched or incorrectly sized pieces.
-
Sewing errors: Improper stitching or assembly requires re-sewing or remaking entire garments.
-
Fitting issues: Achieving the perfect fit requires multiple fitting iterations, each involving creating new samples.
-
Communication delays: Back-and-forth communication with buyers regarding approvals and revisions can further extend the process.
These inefficiencies in the traditional PP sample process can significantly impact small garment factories, leading to missed deadlines, increased costs, and strained relationships with buyers.
Introducing Virtual Sampling:
To address these challenges, the concept of virtual sampling has emerged. Virtual sampling uses 3D modeling and simulation technology to create digital representations of garments, eliminating or significantly reducing the need for physical samples. This approach drastically streamlines the PP sample process, saving time, resources, and money.

The AI Advantage: Streamlining PP Sample Development for Small Garment Factories
Artificial intelligence offers a transformative solution to the inefficiencies of the traditional PP sample process, especially for small garment factories. By implementing AI-powered tools, these businesses can significantly streamline development, reduce delays, and improve overall efficiency.
Here's how AI is changing the game:
3D Virtual Sampling: Replacing Physical Samples with Digital Precision
The cornerstone of AI's impact on PP samples is 3D virtual sampling. This technology uses sophisticated 3D modeling and simulation software to create highly realistic digital representations of garments. Designers and buyers can virtually interact with prototypes instead of relying on physical samples for fit tests and approvals. It offers several key advantages:
-
Elimination or Reduction of Physical Samples: By creating accurate digital twins of garments, 3D virtual sampling significantly reduces, and in some cases eliminates, the need for multiple physical samples. It directly addresses the primary source of delays and costs in the traditional process. For small garment factories, this translates to massive savings in material costs, labor, and shipping expenses.
-
Visualization of All Design Elements: 3D virtual sampling allows for every detail, including different fabrics, colors, prints, sizes, and fits. Designers can experiment with various options virtually, seeing the results in real-time without physical samples for each variation. It empowers small garment factories to offer greater design flexibility to their clients.
-
Virtual Fitting and Fit Adjustments: AI-powered virtual fitting tools allow designers to visualize how a garment will fit on a virtual model with precise body measurements. It eliminates the need for repeated physical fittings and alterations. These are a primary source of delays in the traditional process. Small garment factories can quickly and easily adjust the fit, drape, and silhouette of a garment digitally, ensuring a perfect fit before cutting.
AI-Driven Pattern Making: Automating the Foundation
While 3D virtual sampling addresses the later stages of PP sample development, AI can also streamline the initial pattern-making process. AI algorithms can analyze design specifications and generate accurate patterns automatically, significantly reducing the time and effort required for manual drafting. It is beneficial for small garment factories with limited pattern-making expertise or resources.
Benefits of 3D Virtual Sampling for Small Garment Factories (and Reducing PP Delays):
The benefits of 3D virtual sampling go beyond just faster sample creation; they have a cascading positive effect on the entire production process:
-
Speeding Up Product Development (Weeks Instead of Months): By eliminating the time spent creating and shipping physical samples, 3D virtual sampling can drastically reduce product development time. What used to take weeks or even months can now be accomplished in a fraction of the time, allowing small garment factories to respond quickly to market trends and meet tight deadlines. It directly translates to faster PP approvals and quicker time to market.
-
Accurate Representation of Garment Style and Fit: 3D virtual samples accurately represent the garment's style and fit using precise measurements and realistic fabric simulations. It minimizes the risk of misunderstandings between designers, factories, and buyers, leading to fewer revisions and faster PP approvals.
-
Eliminating Postage and Waiting Time for Physical Samples: The time and cost of shipping physical samples back and forth between factories and buyers are eliminated. It saves money and significantly reduces the overall lead time for PP sample approval.
-
Enabling Quick Changes to Fit and Style: Changes to fit, style, fabric, or color can be made instantly in the virtual environment, allowing for rapid iteration and feedback. This flexibility is invaluable for small garment factories offering customized products and responds quickly to buyer requests.
-
Vastly Reduced Sampling Costs: The reduced need for physical samples translates to significant cost savings in materials, labor, and shipping. It is especially beneficial for small garment factories operating on tight budgets.
-
Usability of Computer-Generated Images for Marketing Materials: The high-quality images generated from 3D virtual samples can be used for marketing materials, such as catalogs, websites, and social media, even before physical samples are ready. Small garment factories can start marketing their products earlier and generate pre-orders.

Addressing the Challenges of Implementing 3D Virtual Sampling (AI) in Small Garment Factories
While the benefits of 3D virtual sampling are substantial, small garment factories may encounter some challenges during implementation. Recognizing and addressing these challenges proactively is key to successful adoption.
Here are the primary challenges and practical solutions for small garment factories:
1. Lack of Skills with 3D Design Software:
Many small garment factories may not have staff with strong traditional pattern-making and sewing skills but lack experience with 3D design software. This skills gap can be a significant hurdle to implementing virtual sampling.
-
Solutions:
-
Training Existing Staff: Investing in training programs for existing staff is often the most cost-effective long-term solution. Many software vendors offer online tutorials, workshops, and certification programs. Focusing training on key personnel, such as pattern makers and sample room staff, can create internal expertise within the small garment factory.
-
Start with Basic Functionality: Rather than trying to master all the advanced features of the software at once, start by focusing on the core functionalities needed for virtual sampling, such as pattern import, basic modeling, and fit simulation. This phased approach makes the learning process less overwhelming.
2. Difficulty Deciding Who Within the Organization Should Handle 3D Content Development:
Small garment factories often have limited staff. They may not have dedicated 3D designers. Deciding who should be responsible for 3D content creation can be a challenge.
-
Solutions:
-
Outsourcing 3D Content Creation: Outsourcing 3D modeling and virtual sample creation to specialized companies or freelance 3D artists is a viable option, especially for small garment factories with limited in-house resources. It allows them to access expert skills without the overhead of hiring full-time staff. Find a reliable partner with experience in the apparel industry.
-
Hiring or Contracting Individuals with 3D Design Expertise: As the demand for 3D virtual sampling grows, hiring or contracting individuals with 3D design expertise becomes a more strategic investment for small garment factories. It provides in-house control over the 3D content creation process and allows for greater flexibility and faster turnaround times in the long run.
-
Cross-Training Existing Staff: A hybrid approach can be potent. Identify staff members with an aptitude for technology and design and provide them with targeted training on 3D software. It can create a small in-house team capable of handling basic 3D tasks while outsourcing more complex projects.
Considerations for Small Garment Factories:
-
Start Small and Scale Up: Begin with a pilot project using 3D virtual sampling for a specific product or style. It allows you to test the technology, train your staff, and refine your workflows before implementing it across the factory.
-
Choose User-Friendly Software: Opt for 3D software that is intuitive and easy to learn, even for users with limited prior experience.
-
Seek Vendor Support: Most 3D software vendors offer excellent customer support, including training materials, tutorials, and technical assistance. Take advantage of these resources.

Benefits of AI for Small Garment Factories: Reducing PP Sample Delays and Accelerating Production
The primary benefit of AI for small garment factories lies in its ability to address the persistent problem of PP sample delays. By streamlining the entire sample development process, AI unlocks significant advantages in speed, cost, communication, and resource allocation.
Here's a detailed look at how AI directly tackles PP sample delays:
-
Faster PP Sample Creation and Approval: The most immediate impact of AI is the significant acceleration of PP sample creation. You can generate virtual samples within hours or days, compared to the weeks often required for traditional physical samples. It achieves it through automated pattern-making, virtual fitting, and realistic 3D visualization. Once created, these virtual samples can be instantly shared with buyers digitally, eliminating shipping time and allowing for immediate feedback. It drastically reduces the time spent waiting for physical samples to be shipped, reviewed, and returned, resulting in much faster PP sample approval.
-
Reduced Lead Times and Faster Time to Market: Quicker PP sample approvals have a cascading effect on the entire production timeline. Small garment factories can significantly reduce overall lead times by eliminating the PP sample bottleneck. The rapid turnaround time allows them to bring new products to market faster, capitalize on emerging trends, and gain a competitive edge. It also improves their ability to meet tight deadlines imposed by buyers.
-
Lower Costs Associated with PP Samples: The traditional PP sample process is inherently expensive due to the need for multiple physical samples. Each iteration requires labor for pattern making, cutting, sewing, and finishing, as well as the cost of materials and shipping. AI-powered virtual sampling drastically reduces these costs by minimizing the need for physical samples. Fewer samples mean less material waste, reduced labor costs, and no shipping expenses. These savings can be substantial for small garment factories operating on tight budgets.
-
Improved Communication and Reduced Misunderstandings: Clear communication between the factory and the buyer is crucial for efficient PP sample approval. 3D visualizations generated by AI software provide a much more detailed representation of the garment than traditional sketches or photographs of physical samples. Buyers can virtually examine the garment from all angles, zoom in on details, and visualize it on a virtual model. This enhanced visualization minimizes misunderstandings and reduces the need for multiple rounds of revisions, further speeding up the approval process.
-
More Efficient Use of Resources: You can reallocate the time and resources saved through AI-driven PP sample development to other critical areas. By reducing the time spent on manual sample creation and revisions, small garment factories can free up their skilled staff to focus on other tasks, such as production planning, quality control, and customer relationship management. This more efficient use of resources increases overall productivity and profitability.

Accelerate Your Production with AI-Powered Solutions from EverLighten
The future of garment manufacturing, especially for small garment factories, is inextricably linked to AI-powered technologies. By streamlining the PP sample process, AI offers a powerful solution to reduce delays, cut costs, and accelerate time to market. Embracing these advancements is no longer a luxury but a necessity for staying competitive in today's fast-paced industry.
If you're ready to explore how AI can revolutionize your PP sample development and accelerate your production, connect with EverLighten. We specialize in custom apparel manufacturing and are committed to helping businesses of all sizes leverage the latest technologies and best practices.
-
100% Customization: We offer complete customization options, allowing you to bring your unique designs to life with precision and quality.
-
100% Quality Check: Our rigorous quality control processes ensure that every garment meets the highest standards.
-
Free Design Help: Our experienced design team can assist you with design development and optimization.
-
Worldwide Delivery: We offer reliable and efficient worldwide shipping to reach your customers globally.
-
24/7 Support: Our dedicated customer support team is available around the clock to answer your questions and provide assistance.
-
Unlimited Revisions: We offer unlimited revisions to ensure you're satisfied with the final product.
-
Low MOQ (Minimum Order Quantity): We offer adaptable MOQs, ensuring businesses of all sizes can access our custom apparel services.
Contact EverLighten today to discuss your garment manufacturing needs and discover how we can help you integrate AI-driven solutions into your workflow for faster PP approvals and accelerated production.
FAQs
1. What specific AI technologies are used for virtual sampling?
Virtual sampling utilizes 3D modeling software, CAD (Computer-Aided Design), and AI algorithms. These algorithms simulate fabric drape, fit, and movement, creating realistic digital representations of garments.
2. How much can AI reduce PP sample development time?
The time savings can be significant, potentially reducing PP sample development time from weeks to a few days. It depends on the complexity of the garment and the specific AI tools used.
3. Is it expensive to implement AI for PP sample creation?
The cost of implementation varies depending on the chosen software and the level of integration. However, cloud-based solutions and subscription models make these technologies more accessible to small garment factories. The cost savings from reduced material waste, labor, and shipping often offset the initial investment.
4. Do I need specialized AI experts to use these technologies?
While some technical expertise is helpful, many AI-powered tools are user-friendly and require minimal specialized training. Software vendors typically offer training resources and support.
5. How does AI improve communication with buyers during the PP sample process?
3D visualizations generated by AI software provide a more detailed representation of the garment than traditional methods. Buyers can virtually examine the garment from all angles and request changes digitally, reducing misunderstandings and speeding up the approval process.