A Breakdown of Custom Plush Toys Manufacturing Wait Times
| Apr, 06 , 24
Imagine the pure joy of cuddling your creation – a custom plush toy designed to your specifications! You have poured your creativity into the perfect design. Now, you can't wait to hold the finished product. But, amidst the excitement, a question inevitably pops: "How long will it take for my adorable custom plushie to arrive?"
We understand your eagerness! The wait can feel agonizing when you want to snuggle with your customized plushie masterpiece. Before you hit the refresh button on your order status page a hundred times, let's delve into the world of custom plush toy production timelines. Several factors come into play, and understanding them can help you appreciate the artistry behind your soon-to-be cuddly companion. From meticulous design development to quality control checks, each step contributes to a custom plushie that's not just cute but built to last.
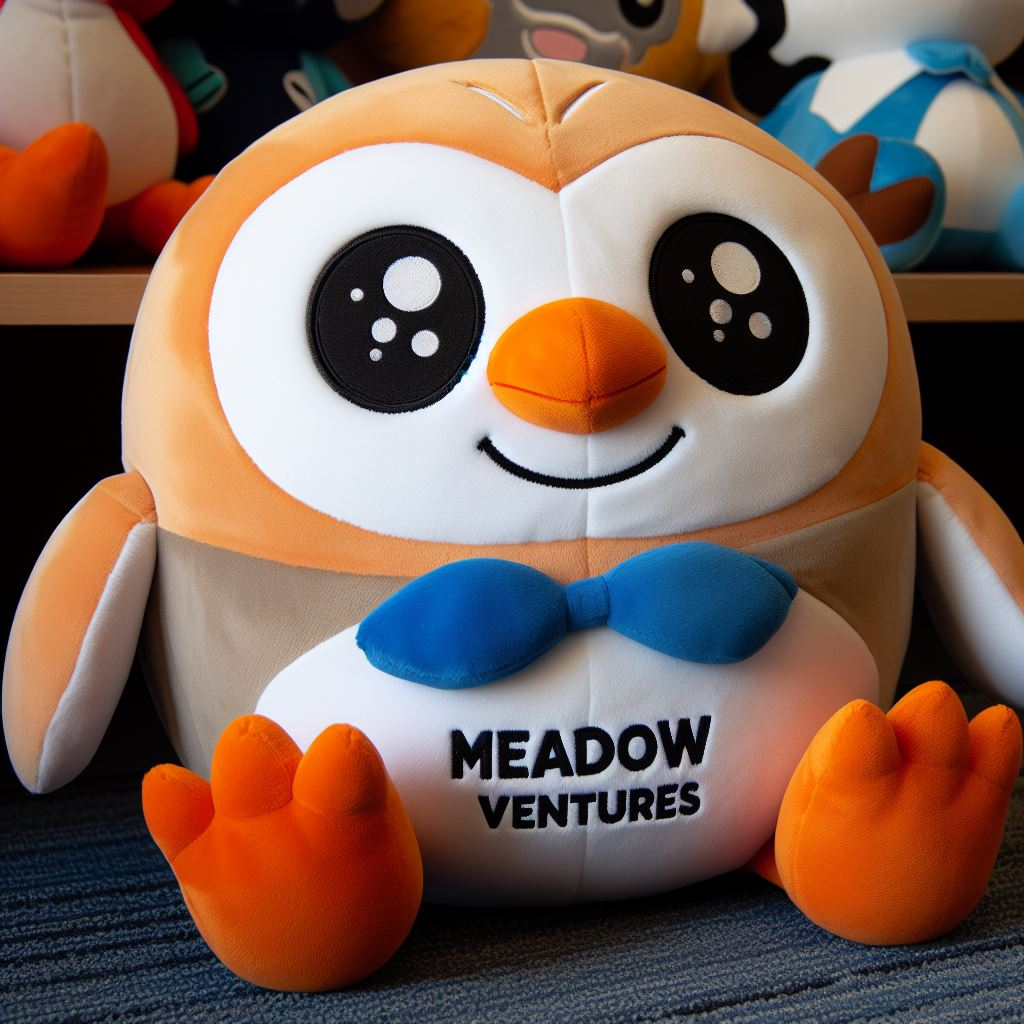
The Art of Crafting Cuteness: Behind the Scenes,
This section dives behind the curtain to reveal the custom plush toy journey from concept to cuddle. We'll explore the various stages in its creation, each playing a vital role in bringing your fluffy friend to life.
Design Development: From Sketch to Snuggle-Worthy Blueprint
The journey of your custom plush begins with the spark of an idea! The initial stage, design development, is about translating your vision into a clear and concise blueprint for the manufacturer. It's a collaborative process often involving consultations with experienced designers to refine your concept and ensure its feasibility. Here's a breakdown of this crucial first step:
Consultation:
- Brainstorming Session:
- It is where you get to unleash your creativity! Share your initial ideas, sketches, or reference images with the designer.
- Discuss the purpose of the Custom plush – is it a mascot, a gift, or a promotional item? Knowing its intended use helps create a design that aligns with your goals.
- Design Expertise:
- The designer will offer valuable insights and suggestions based on their experience.
- They can help refine your design for production feasibility, suggest materials that best suit your vision, and ensure the design translates well to a Custom plush format.
- Technical Considerations:
- Discussing details like size, complexity, embroidery options, and color palette is crucial. The designer will advise on limitations and suggest alternatives to ensure your custom plushie is adorable and producible within your budget.
Finalization:
- Mockups and Refinements:
- The designer will create digital mockups of your custom plush toy. These mockups allow you to visualize your design in 3D, providing an opportunity to request any changes or adjustments.
- This back-and-forth refinement process continues until you're satisfied with the final design.
- Technical Specifications:
- Once you finalize the design, the designer will create a technical specification sheet. It documents details of every element of your custom plush toy, including:
- Dimensions and proportions
- Material specifications for fabric, stuffing, and any additional elements
- Pantone color references for accurate color reproduction
- Embroidery details, stitch types, and thread colors (if applicable)
- Any special features or functionalities
Additional Considerations:
- Copyright and Licensing:
- If your design incorporates licensed characters or copyrighted material, ensure you have the necessary permissions for commercial use.
- Minimum Order Quantities (MOQs):
- Many manufacturers have minimum order quantities (MOQs) – the minimum number of Custom plushies you can order per design. Be aware of these requirements and plan your production accordingly.
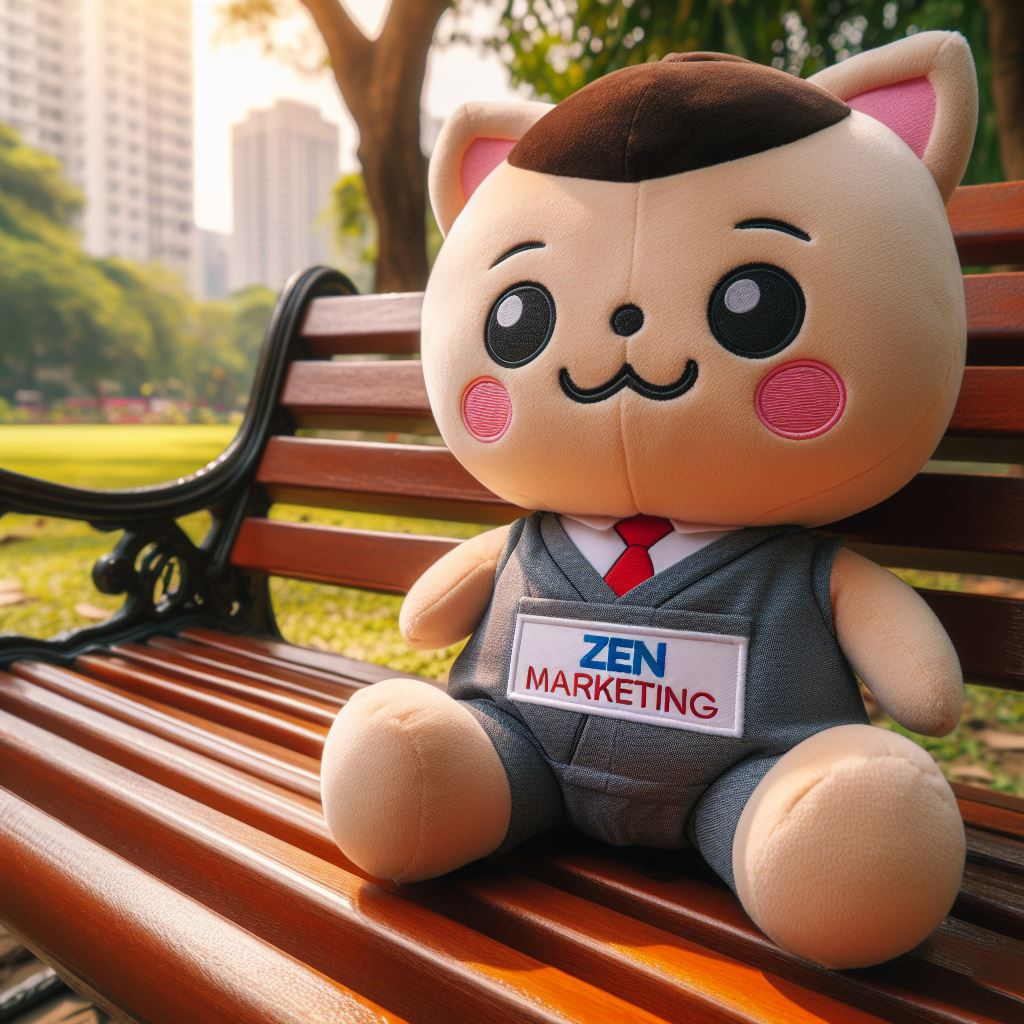
Material Selection: Building the Perfect Custom Plushie from the Inside Out
The heart and soul of your custom plushie lies not just in the blueprint but in the materials chosen to bring it to life. Material ensures your custom plushie is adorable but safe, soft, durable, and perfect for those countless cuddles.
Fabric Sourcing: A Quest for Quality and Cuddlability
- Material Options:
- A wide variety of fabrics are available for Custom plushie creation, each offering unique advantages:
- Custom plush Fabrics: These soft, cuddly fabrics are the most common choice, coming in various textures (fleece, minky, etc.) and pile lengths.
- Cotton Twill: This durable fabric is ideal for Custom plushie accessories like clothing or hats.
- Faux Fur: For a luxurious touch, faux fur can add a realistic and visually appealing element.
- The designer will recommend fabrics that best suit your design and desired feel (soft, smooth, textured).
- Safety First:
- Reputable manufacturers prioritize safety, using only fabrics that meet stringent safety regulations. These often include certifications for flammability resistance, absence of harmful chemicals, and colorfastness (ensuring colors don't bleed).
- Experts test the materials to ensure they're safe for all ages, especially children.
- Sourcing and Sustainability:
- Manufacturers committed to sustainability might offer eco-friendly fabric options made from recycled materials.
- You can inquire about the origin and certifications of fabrics to align with your sustainability preferences.
Quality Checks: A Meticulous Eye for Perfection
Before any fabric hits the production floor, it undergoes a series of rigorous quality checks:
- Visual Inspection:
- Experts test the fabric rolls for any defects like tears, snags, or inconsistencies in color or texture.
- Only flawless fabric cuts your custom plush.
- Lab Testing:
- Fabric samples are sent to independent labs for testing to ensure they meet safety standards (flammability, chemical content) and colorfastness requirements.
Additional Considerations:
- Matching Colors Accurately:
- Pantone color references ensure the chosen fabric accurately reflects the colors in your design.
- Some manufacturers might offer dye sublimation printing the fabric for intricate designs or logos.
- Stuffing Selection:
- The type of stuffing is vital in the softness, huggability, and overall shape.
- Regular stuffing options include hypoallergenic polyester fiberfill, recycled plastic bottles (eco-friendly option), and even memory foam for a luxurious feel.
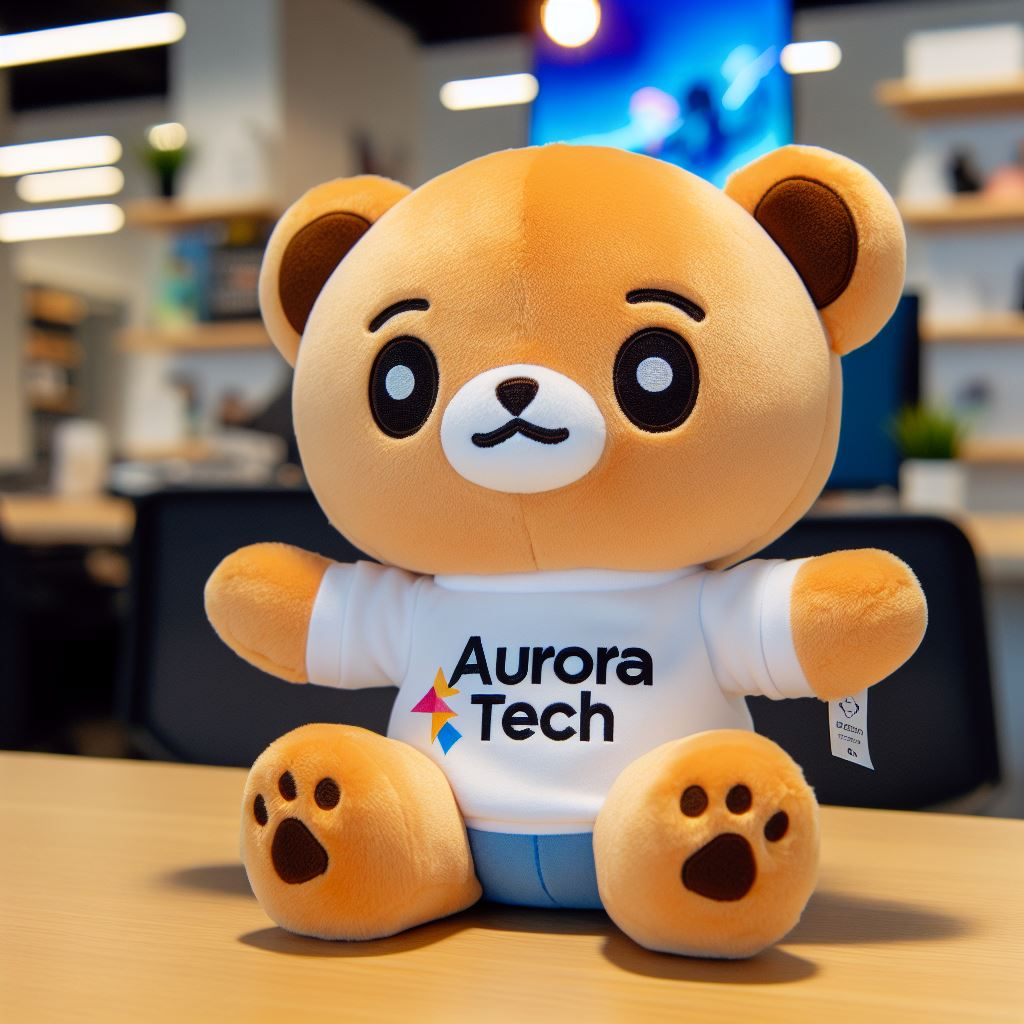
Pattern Creation and Development: Transforming Your Design into a Custom Plushie Puzzle
The magic of transforming your flat illustration into a huggable 3D friend comes alive in pattern creation and development. The intricate process involves skilled artisans translating your design into a precise roadmap for the custom plush's construction.
From Sketch to Blueprint:
- Understanding the Design:
- The pattern maker meticulously analyzes your finalized design, paying close attention to every detail – size, proportions, curves, and special features like pockets, horns, or tails.
- Deconstructing the Design:
- The design is then deconstructed into individual pieces, like the front body panel, back panel, limbs, ears, and additional elements. Each piece is visualized as a flat pattern piece that, when assembled, will form the complete custom plushie.
- Software and Expertise:
- Specialized software creates these flat pattern pieces. The software allows for precise scaling, mirroring (ensuring symmetrical shapes), and seam allowances (accounting for fabric thickness during sewing).
- The Art of Seam Allowance:
- Seam allowances are crucial for achieving a clean and well-finished custom plush. The pattern maker will factor in the appropriate seam allowance based on the fabric type and desired final look.
Bringing the Pieces Together:
- Prototyping for Perfection:
- In some cases, a paper prototype might be created to test the fit and functionality of the individual pattern pieces before moving on to fabric. This allows for adjustments to be made before the precious fabric is cut.
- Marking and Efficiency:
- Once the digital pattern is finalized, it's used to create physical paper patterns or markers. These markers are used to efficiently cut the fabric pieces with minimal waste.
- Matching and Mirroring:
- The pattern maker ensures the correct placement of directional fabrics (with specific patterns) and mirrors the design for symmetrical elements like ears or legs.
Additional Considerations:
- Complexity and Customization:
- The complexity of your design directly affects the pattern-creation process. Simple custom plushie shapes require less intricate patterns, while intricate designs with multiple pieces and details require more complex patterns.
- Hidden Seams and Closures:
- The pattern maker strategically plans seam placements to minimize their visibility on the finished product. Hidden closures (like Velcro or zippers) are incorporated for stuffing access while maintaining a clean aesthetic.
- Articulation (Optional):
- For Custom plushies with movable limbs or features, the pattern maker will create specialized joint systems using additional materials or specific stitching techniques.
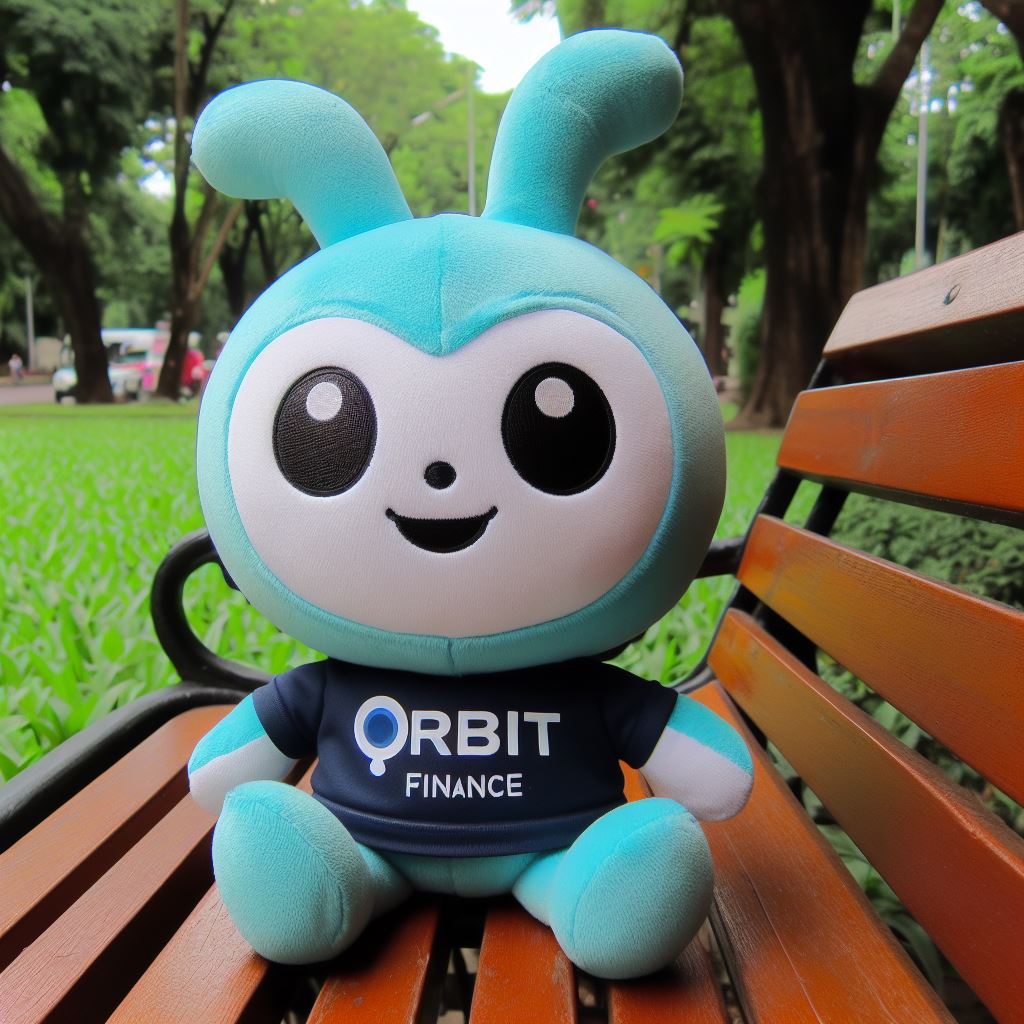
Sample Creation and Approval Cycles: A Glimpse into Your Custom Plushie Prototype
Imagine the thrill of seeing your custom plush design translated into a tangible prototype! The sample creation and approval cycle offers a chance to witness your vision come to life, allowing for refinements before full-scale production commences. Here's a closer look at this crucial stage and the typical workflow:
Bringing Your Design to Life (The Sample Creation Process):
- Translating the Plan:
- Using the finalized design and technical specifications, skilled artisans meticulously cut fabric pieces based on the approved patterns.
- The Art of Sewing:
- Experienced seamstresses carefully sew the pieces together, taking special care to ensure all seams are secure and meet quality standards.
- Stuffing with Love:
- The custom plush is then stuffed with the chosen hypoallergenic filling material, ensuring the desired squishiness and shape retention.
- Embroidery and Finishing Touches:
- Any embroidery details, like facial features or logos, are carefully stitched onto the custom plush. Finishing touches like buttons, ribbons, or custom accessories are applied according to the design.
The Power of Prototypes:
- Visualizing the Final Product:
- The completed sample provides a realistic representation of your final custom plush. You can assess its size, proportions, color accuracy, and aesthetic appeal.
- Identifying Potential Issues:
- The sample allows you to identify any potential issues before mass production begins. It could be minor adjustments to seam placement, color discrepancies, or slight differences in shape compared to the original design.
The Approval Process: Collaborative Refinement
- Communication is Key:
- Once you receive the sample, a clear communication channel is established with the manufacturer. Discuss any feedback or desired adjustments with the dedicated project manager.
- Revisions and Re-Sampling (Optional):
- Based on your feedback, the manufacturer might offer minor revisions to the sample. In some cases, a re-sample might be created to ensure you're completely satisfied before moving on to production.
Additional Considerations:
- Lead Time and Costs:
- Sample creation typically incurs a separate fee and adds some lead time to the production process. Be aware of these factors and plan accordingly.
- Sample Retention:
- Some manufacturers might offer to send you the sample for review, while others retain it for future reference. Discuss this with the manufacturer beforehand.

Production: From Fabric to Finished Friend - The Assembly Line of Cuteness
The magic truly unfolds in the production stage, where your custom plush toy design transforms from meticulously crafted patterns and carefully chosen materials into the adorable cuddle companion you envisioned. This stage involves a symphony of skilled workers and specialized equipment, all working together to bring your custom plush to life.
The Cutting Edge: Fabric Transformation
- Efficiency Reigns Supreme:
- Using the finalized patterns (often digitally stored), specialized cutting machines efficiently cut multiple layers of fabric simultaneously. It minimizes fabric waste and ensures consistency in shape across all custom plushie pieces.
- Marking for Accuracy:
- In some cases, fabrics might be manually marked with seam allowances or stitching guidelines to further aid in the sewing process.
Sewing with Skill: Building the Custom Plushie Body
- Assembly Line Expertise:
- Experienced makers take over, working on dedicated sewing machines to assemble the individual pieces of your custom plush.
- Stitch Type Selection:
- They might use various stitches per the fabric type and desired seam strength. Regular options include straight stitch, zig-zag stitch, and French seam (for a clean, finished look on the inside).
- Quality Control Throughout:
- As different sections of the custom plush are sewn together, quality control checks are conducted at regular intervals. It ensures proper seam construction and adherence to the design specifications.
Stuffing with Love: Achieving the Perfect Squish
- Filling Up the Fun:
- Once the main body of the custom plush is assembled, it's time for the stuffing! Skilled workers carefully fill the custom plush with the chosen hypoallergenic stuffing material.
- Density Control:
- The amount of stuffing used is carefully monitored to achieve the desired squishiness and maintain the intended shape of the custom plush.
Finishing Touches: Bringing the Design to Life
- Embroidery Expertise:
- Skilled embroidery artists use specialized machines to stitch facial features, logos, or any other intricate details onto the custom plush, breathing life into your design.
- Attention to Detail:
- Buttons, ribbons, custom accessories, or other embellishments are carefully attached according to the design specifications.
- Final Inspection and Packaging:
- The finished custom plush undergoes a rigorous final inspection to ensure all seams are secure, the stuffing is even, and all details are present and flawless.
- Once approved, your custom plush is lovingly packaged and prepared for shipment.
Additional Considerations:
- Production Line Efficiency:
- Depending on the complexity of your design and the order quantity, the production process might be further optimized with specialized equipment or dedicated teams for specific tasks (cutting, sewing, stuffing, etc.).
- Customization Options:
- Some manufacturers might offer additional customization options during production, such as custom hang tags, printed ribbons, or personalized packaging – adding a special touch to your custom plushie creation.
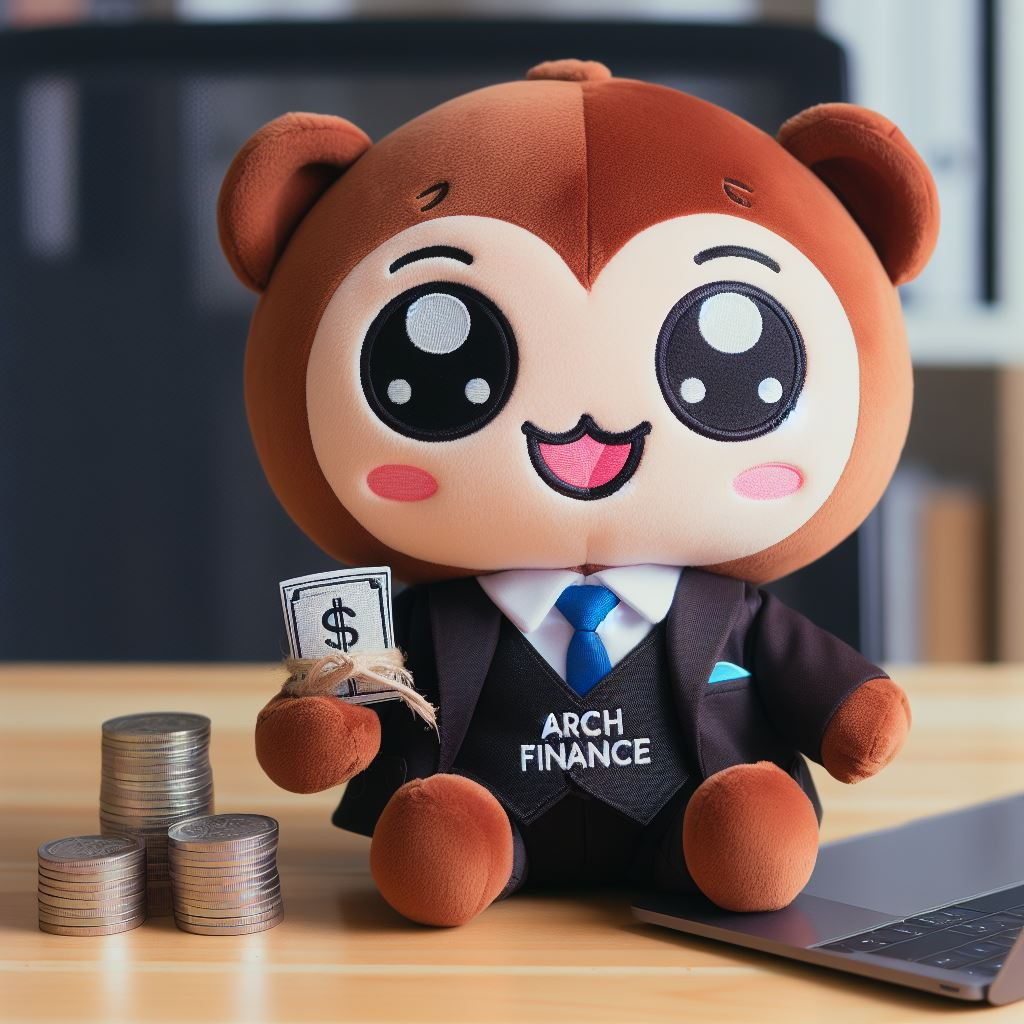
Quality Control Checks: Ensuring Your Custom plushie is Perfect from Paw to Stitch
While the entire custom plush production process prioritizes quality, dedicated quality control checks act as a safety net, guaranteeing your finished custom plush meets the highest safety, craftsmanship, and adherence to your design.
Multi-Layered Scrutiny:
QC checks are not a singular event but a series of inspections happening throughout the production, catching any potential issues early on.
- Pre-Production Checks:
- Material Inspection: They inspect the fabric rolls and stuffing materials for any defects like tears, inconsistencies, or non-compliance with safety regulations.
- Pattern Verification: The production team double-checks the patterns against the approved design specifications to ensure accuracy, proportions, and seam allowances.
- In-Line Checks:
- Seams and Stitching: Inspectors ensure seams are secure and utilize the correct stitch type as specified.
- Stuffing Distribution: Workers monitor the amount of stuffing used to guarantee the desired level of squishiness and proper shape retention.
- Embroidery and Finishing Touches: Experts check the embroidery details, button placement, and additional embellishments for accuracy and adherence to the design.
- Final Inspection:
- Flaw Detection: The finished Custom plush undergoes a rigorous final inspection for any flaws, including:
- Missed stitches or loose seams
- Uneven stuffing distribution
- Misaligned or missing embroidery details
- Inconsistent color tones or fabric discrepancies
- Presence of all required safety features (e.g., flame retardant labels)
Beyond Visual Inspection:
- Safety Testing:
- Random samples might undergo additional safety testing in independent labs for specific markets or age groups (especially for children's toys). It can include flammability testing, chemical content analysis, and small parts testing for choking hazards.
The Importance of Stringent QC:
- Safety First:
- Rigorous QC checks prioritize the safety of the end user, especially children. Ensuring materials meet safety standards and no choking hazards or loose parts is paramount.
- Quality You Can Cuddle:
- QC checks guarantee a well-constructed custom plush with neat and secure stitching, even stuffing distribution, and a flawless finish. It translates to a more durable and visually appealing product.
- Meeting Your Expectations:
- By meticulously checking every detail, QC ensures the final custom plush accurately reflects your design and meets your specific requirements.
Additional Considerations:
- Documentation and Traceability:
- Reputable manufacturers maintain detailed QC records, documenting any checks performed and ensuring the traceability of materials used in your custom plush.
- Continuous Improvement:
- Leading manufacturers utilize QC data to identify areas for improvement in the production process, consistently striving for higher quality standards.
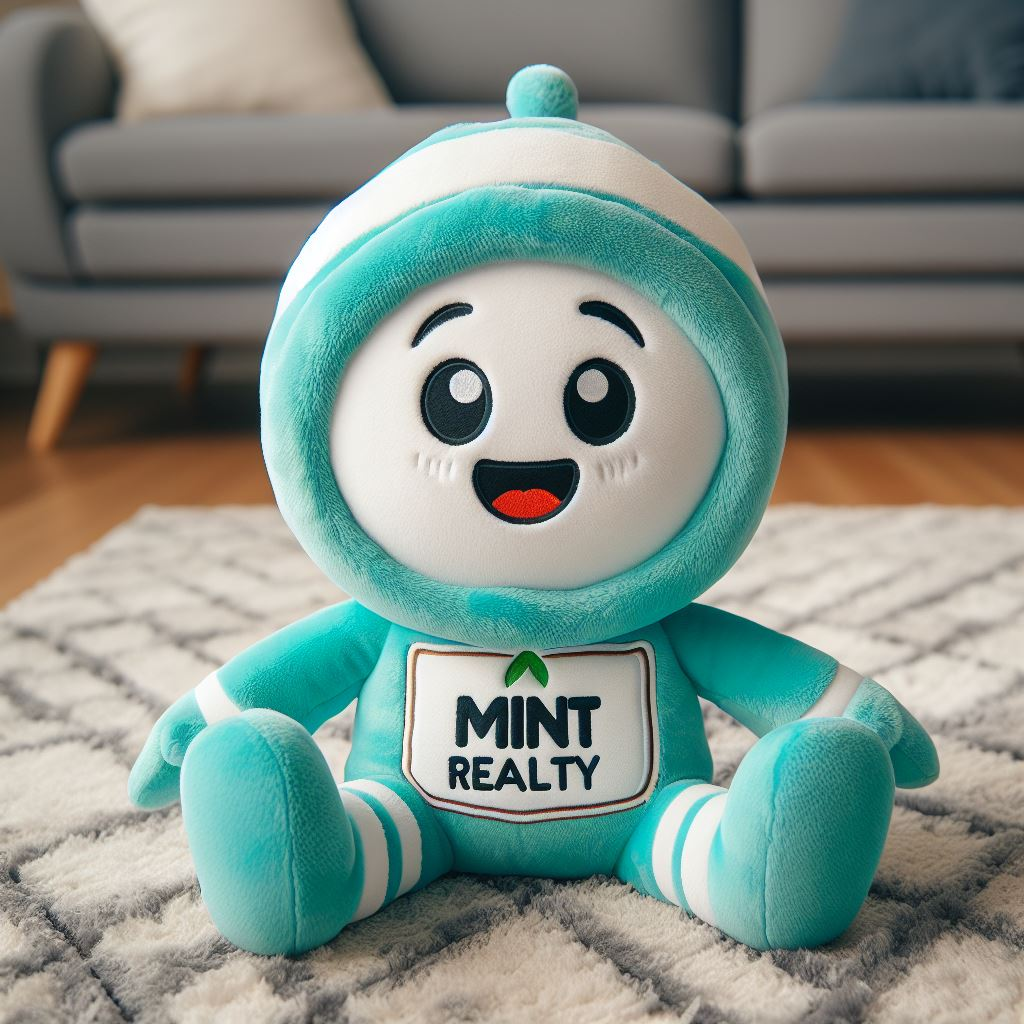
Understanding the Wait: Key Factors Affecting Timelines
This section unveils the secrets behind custom plush production timelines. We'll explore the key factors that can influence how long it takes for your adorable creation to arrive:
Complexity of Design: Unveiling the Impact on Custom Plush Production Timelines
The world of custom plushie creation thrives on imagination! However, the intricate details you envision can significantly influence the production timeline. Let's delve deeper into how design complexity impacts the time it takes for your cuddly companion to come to life:
Simple Shapes, Speedy Production:
- Basic Designs: Custom plushies with simple shapes like squares, circles, or animals typically require less time. Fewer pattern pieces translate to quicker cutting, sewing, and assembly.
- Limited Details: Designs with minimal facial features (embroidered eyes and smiles) or no additional elements like pockets or hats require less time for embroidery and finishing touches.
Intricacy Takes Time, But Creates Cuddly Masterpieces:
- Multiple Pieces and Seams: Custom plushies with intricate shapes, multiple limbs, or detailed features like wings, horns, or tails involve more pattern pieces. It leads to a long cutting and sewing process as each piece needs to be meticulously assembled.
- Embroidery Extravaganza: Elaborate embroidery details for facial features, logos, or intricate patterns require more time and skilled artistry. The complexity of the design directly affects the embroidery time.
- Special Techniques and Materials: Custom plushies with unique features like posable limbs, light-up elements, or customized sound modules involve additional techniques and materials, extending the production timeline.
Finding the Sweet Spot Between Creativity and Time:
- Collaboration is Key: Discussing your design with the manufacturer helps identify potential time-saving adjustments. Simplifying minor details without compromising the overall look can streamline production.
- Breaking Down Complexity: Decomposing intricate designs into smaller, simpler elements can expedite the process. It allows for the efficient production of individual components and their final assembly.
Additional Considerations:
- Sample Creation and Revisions: Complex designs often require multiple sample rounds to ensure detailed execution. Be prepared for potential delays associated with sample creation and feedback loops.
- QC Scrutiny: Intricate designs undergo rigorous quality control checks to ensure every detail aligns with the approved design. The additional scrutiny contributes to a slightly longer timeline.
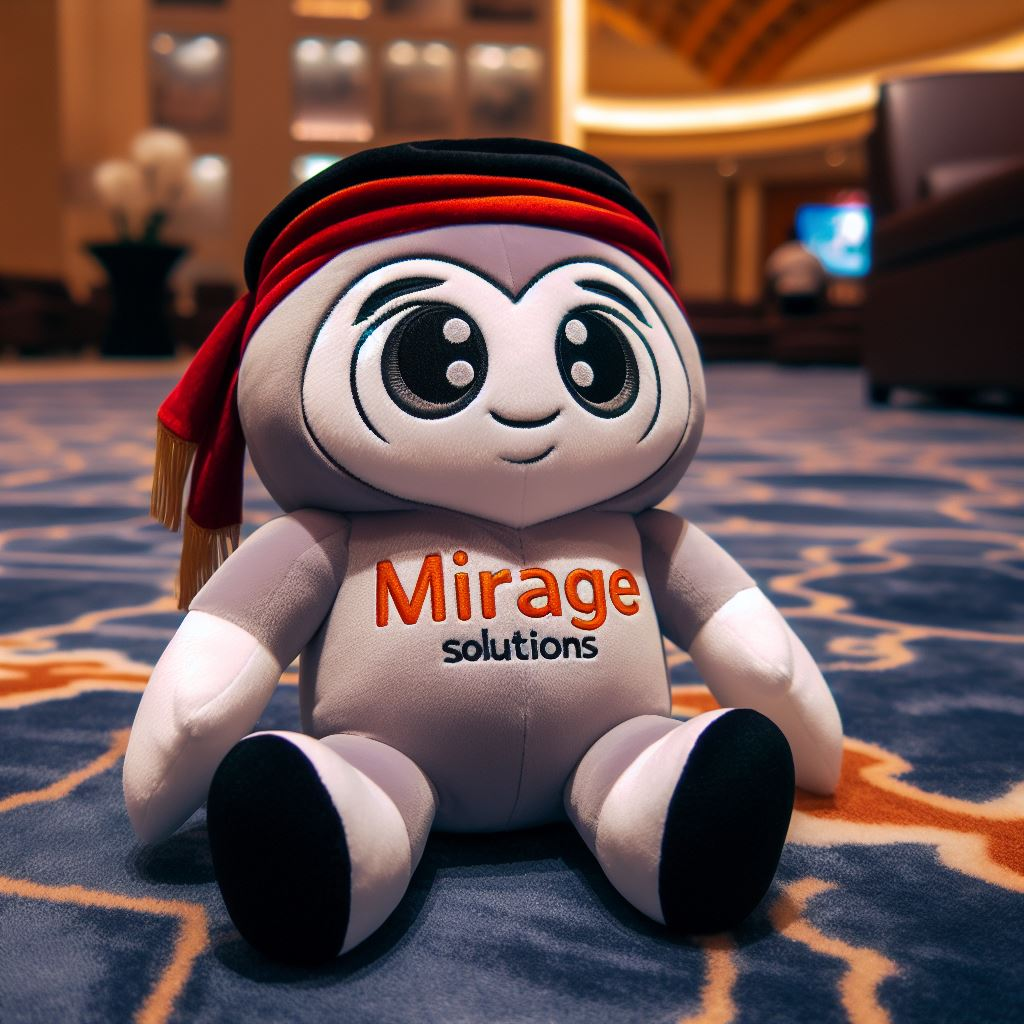
Order Quantity: The Balancing Act of Customization and Production Speed in Custom plushie Creation
The allure of custom plushie creation extends beyond the design itself. The ability to order a single, unique custom plush or a large batch for promotional purposes adds another layer of flexibility. However, the quantity you order directly impacts the production timeline.
Single Custom Plush Serenity: A Swift and Special Creation
- Streamlined Production: Ordering a single custom plush eliminates the need for mass production techniques. It allows skilled artisans to focus on meticulously crafting your unique creation, often leading to a faster turnaround time.
- Reduced Complexity: Single-custom plush orders often involve simpler designs or limited embroidery details, further streamlining the production process compared to large batches.
Bulk Orders: Building a Custom plushie Army (But with a Wait)
- Economies of Scale: Ordering larger quantities allows manufacturers to leverage economies of scale. Bulk fabric purchases, efficient cutting processes, and dedicated production lines for specific tasks can translate to cost savings per custom plush.
- Increased Production Time: Larger orders require more materials, labor, and potentially additional production runs. It can extend the timeline compared to a single custom plush.
- Quality in Quantity: Reputable manufacturers maintain the same high-quality standards for all order sizes. The wait might be longer, but you can be confident each custom plush in your bulk order will be well-crafted and meet your specifications.
Finding Your Perfect Order Size:
- Consider Your Needs: Are you creating a one-of-a-kind gift or a promotional giveaway for thousands? Understanding your purpose can help determine the ideal order quantity.
- Budgeting for Quality: While bulk orders offer cost savings, prioritize quality over extreme cost-cutting. Choose a reputable manufacturer known for using safe materials and maintaining high standards.
- Planning Makes Perfect: Placing your order well in advance, especially for large quantities, allows the manufacturer to schedule production efficiently and meet your desired delivery date.
Additional Considerations:
- Minimum Order Quantities (MOQs): Many manufacturers have minimum order quantities (MOQs) – the minimum number of Custom plushies you can order per design. Be aware of these requirements and plan your order accordingly.
- Inventory Management: Discuss inventory management options for large, recurring orders. It can help ensure a steady supply of custom plushies without long wait times between orders.
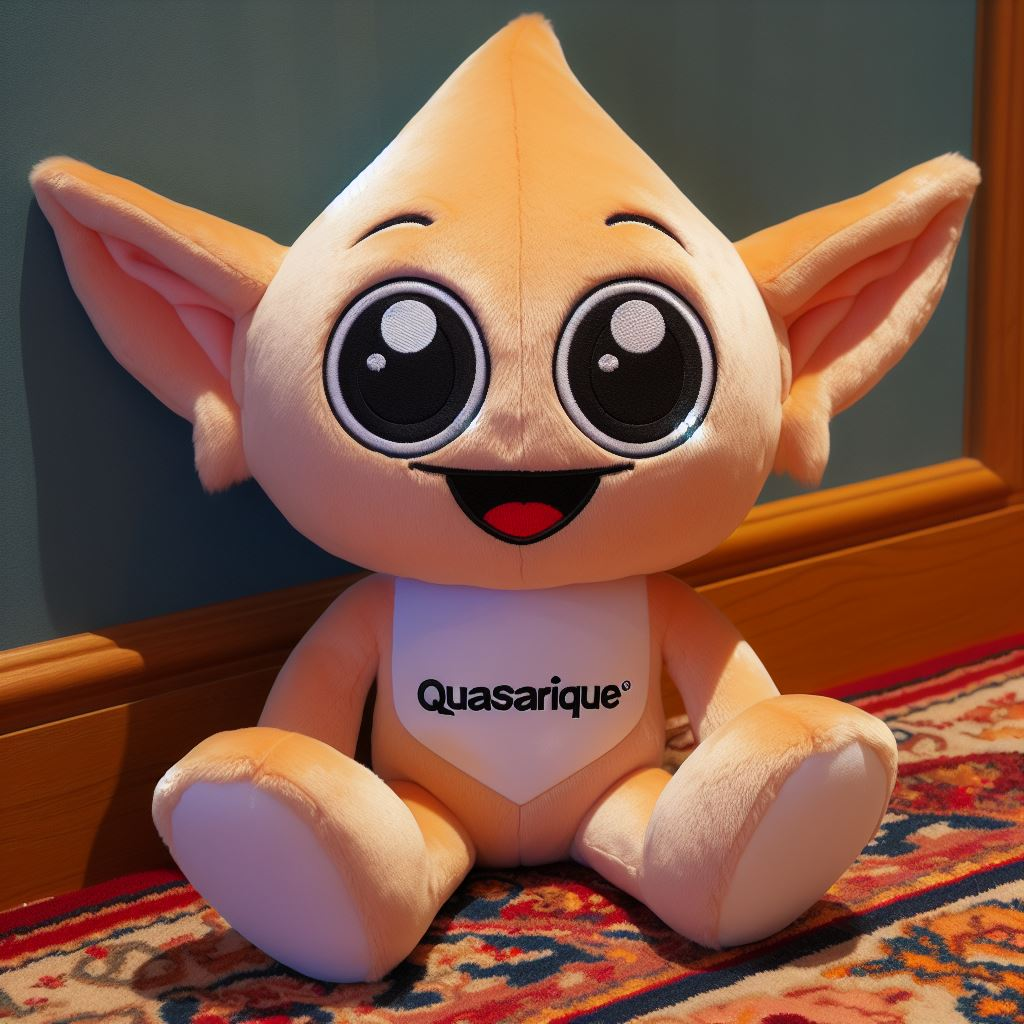
Material Availability: A Balancing Act Between Creativity and Timeliness in Custom Plushie Creation
Custom plushie creation thrives on imagination, but translating those dream designs into reality hinges on the materials you envision. While manufacturers offer many fabrics, fillings, and embellishments, specific choices can impact your production timeline.
Readily Available Fabrics: A Speedy Start to Custom Plushies
- Classic Choices: Common custom plush fabrics like fleece, minky, or cotton twill are available in many colors and textures. It allows for swift production as there's no need to source or wait for specialized materials.
- Seasonal Staples: Many manufacturers stock seasonal fabrics (e.g., holiday prints and specific color trends) to cater to popular demands. Production can proceed without delays if your design aligns with these readily available fabrics.
Unique Materials: The Allure of the Wait
- Specialty Fabrics: For a truly unique custom plush, you might desire specialty fabrics like faux fur with a specific texture, glow-in-the-dark materials, or metallic accents. Sourcing these less common materials can extend the wait time.
- Custom Printing: If your design incorporates intricate logos or artwork that requires custom printing directly onto the fabric, additional lead time might be necessary for printing and fabric preparation.
Filling Options and the Perfect Squish:
- Classic Stuffing: Common hypoallergenic polyester fiberfill is readily available and allows quick production.
- Eco-Friendly Alternatives: Some manufacturers offer recycled plastic bottles as stuffing material. However, sourcing large quantities of these eco-friendly alternatives might add a slight wait.
- Specialty Fillings: Specific needs, like memory foam for a luxurious feel or weighted stuffing for therapeutic purposes, might require additional sourcing time due to lower demand or specialized suppliers.
Embracing the Wait for the Perfect Touch:
- Customization Through Embellishments: Buttons, ribbons, or custom keychains can add a personal touch to your custom plush. However, sourcing unique embellishments might require additional time than readily available options.
- Planning Makes Perfect: Discussing your desired materials with the manufacturer early allows them to assess availability and provide an accurate timeline estimate.
- Alternatives and Inspiration: Reputable manufacturers can suggest alternative materials that achieve a similar look and feel if your desired option faces delays.
Additional Considerations:
- Seasonal Demands: Certain materials might experience increased demand during specific seasons. Ordering a custom plush with seasonal fabric during the off-season could lead to a slightly longer wait.
- Minimum Order Quantities (MOQs): Some specialty fabrics might have minimum order quantities (MOQs) – the minimum amount a supplier is willing to sell. It can impact production efficiency for smaller orders.
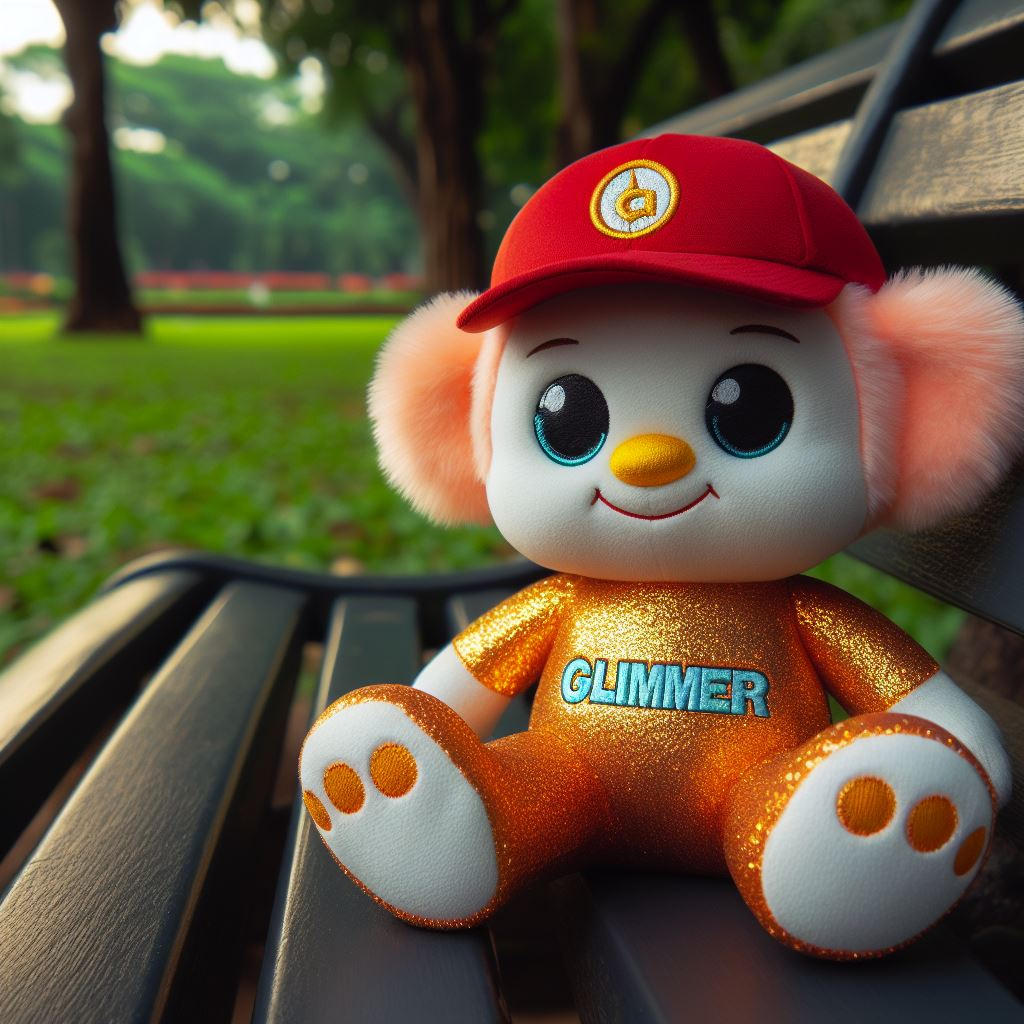
Production Schedule: Unveiling the Journey of Your Custom Plush
The wait for your custom plush can feel agonizing, but understanding the production schedule behind the scenes can transform anticipation into informed excitement. The section delves into the intricate dance between various stages of production, revealing how your cuddly companion comes to life:
From Design Approval to Production Planning:
- The Green Light: Once you finalize your design and receive approval from the manufacturer, the production planning process begins.
- Material Sourcing: The manufacturer sources the necessary fabrics, stuffing, and additional embellishments based on your specifications. Factor in lead times for specialty materials into the overall schedule.
- Pattern Development: Skilled pattern makers meticulously translate your design into precise digital patterns for efficient cutting and sewing.
The Symphony of Production:
- Scheduling the Steps: The production team meticulously schedules each stage of production, considering factors like order quantity, complexity of design, and machine availability. It ensures a smooth flow and minimizes delays.
- Cutting with Precision: They cut the fabric using specialized machines or by hand (for intricate designs) based on the approved patterns.
- Sewing with Skill: Experienced makers meticulously assemble the individual pieces of your custom plush, ensuring secure seams and adherence to the design specifications.
- Stuffing for the Perfect Squish: The chosen stuffing material is carefully measured and distributed to achieve the desired squishiness and maintain the intended shape of the custom plush.
Bringing Your Design to Life:
- Embroidery Expertise: Skilled embroidery artists utilize specialized machines to stitch facial features, logos, or any other intricate details onto the custom plush, breathing life into your design.
- Embellishment and Finishing Touches: They attach buttons, ribbons, custom accessories, or other embellishments according to the design specifications.
- Quality Control Throughout Rigorous quality control is conducted at various stages of production to ensure all elements meet safety standards and adhere to your design.
The Final Stretch: Inspection, Packaging, and Shipment:
- Final Inspection: The completed custom plush undergoes a final, thorough inspection for any flaws in stitching, stuffing distribution, or missing details.
- Packaging with Care: It ensures it arrives safely at your doorstep, ready for a lifetime of cuddles.
- Shipment and Tracking: Your custom plush is shipped using the chosen shipping method, and you typically receive tracking information to follow its journey.
Understanding the Timeline:
- Production Time vs. Shipping Time: The production schedule focuses on the time it takes to create your custom plush. Factor in additional time for shipping based on the chosen method and your location.
- Communication is Key: Reputable manufacturers keep you updated on the progress of your order throughout the production schedule. Don't hesitate to reach out with any questions.
Additional Considerations:
- Bulk Orders and Lead Times: Larger orders might require additional scheduling adjustments within the production line. Be prepared for slightly longer lead times for bulk orders than single-custom plush creations.
- Holiday Seasons and Busy Periods: During peak production times or holidays, manufacturers might experience higher order volumes. Placing your order well in advance ensures your custom plush is incorporated into the production schedule efficiently.
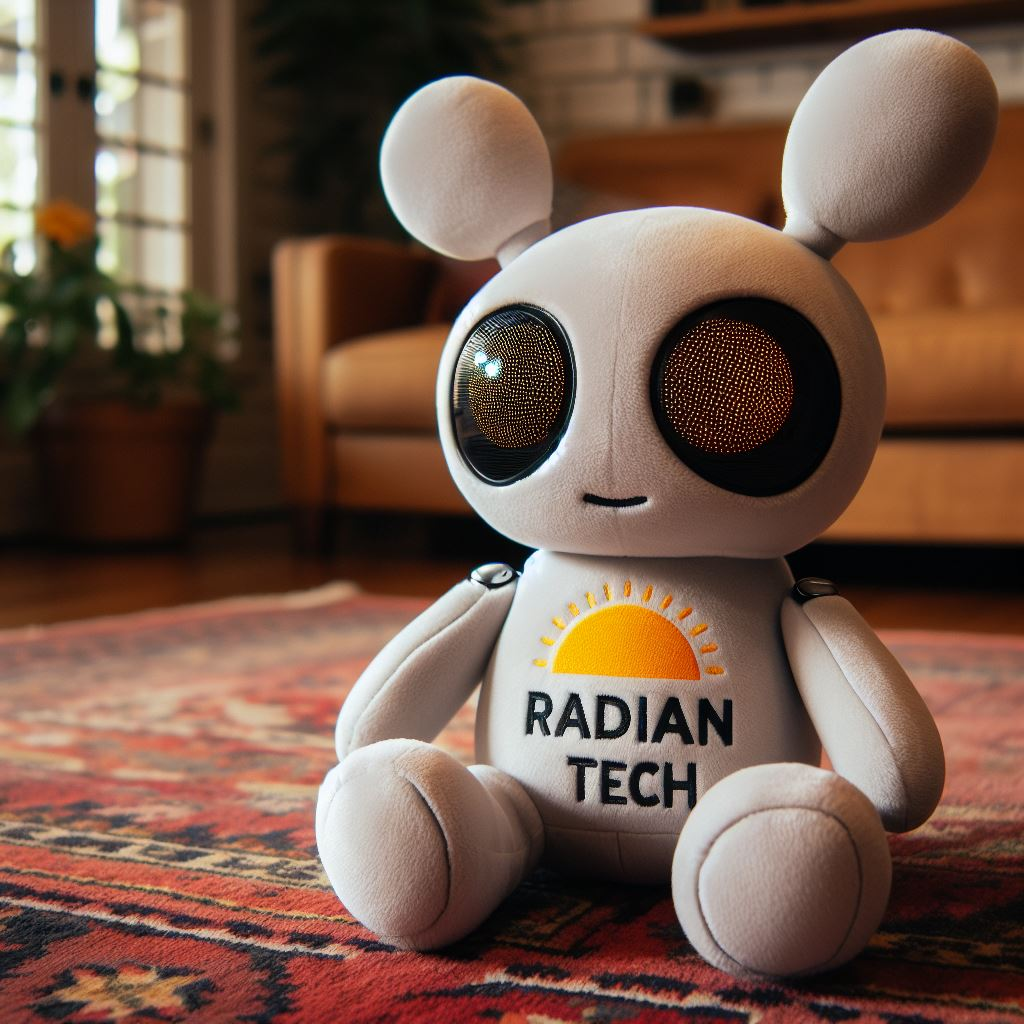
The Final Hurdle: Understanding Shipping Options for Your Custom Plush
The excitement of receiving your custom plush builds as it journey from the production line to your doorstep. This section dives into the world of custom plush toy shipping, exploring the various options available and factors to consider when making your choice:
A Spectrum of Shipping Speeds:
- Express Delivery: For the ultimate in speed, express shipping options like overnight or expedited delivery can get your custom plush to you within a few days, perfect for last-minute gift needs. However, these options typically come at a premium cost.
- Standard Shipping: The most common and cost-effective option, standard shipping usually takes a week or two for your custom plush to arrive. This is a great balance between speed and affordability for most custom plush orders.
- Economy Shipping: The most budget-friendly option, economy shipping can take several weeks for delivery. This might be suitable if you're not in a rush and prioritize saving costs.
Choosing the Right Speed:
- Consider Your Needs: Do you need your custom plush for a specific event? Prioritize speed if you have a deadline, or opt for standard or economy shipping for more relaxed delivery timeframes.
- Budgeting for Delivery: Shipping costs are typically added to the overall price of your custom plush. Weigh the urgency of receiving your custom plush against the additional cost of expedited shipping.
- Location, Location, Location: Your location and the distance from the manufacturer's facilities significantly impact shipping times. Consider this factor when choosing your shipping speed.
Tracking Your Custom Plushie's Adventure:
- Peace of Mind with Tracking: Most reputable manufacturers provide tracking information once your custom plush is shipped. This allows you to monitor its journey and estimate its arrival date.
- Understanding Tracking Updates: Tracking information might not update daily, especially for economy shipping options. Be patient, and your custom plush will soon be in your loving arms.
Additional Considerations:
- International Shipping: Shipping a custom plush can take longer and involve additional customs fees. Ensure you understand the potential costs and estimated delivery times before placing your order.
- Shipping Restrictions: Certain countries might have restrictions on specific materials used in custom plush toys. Discuss this with the manufacturer beforehand to avoid any delays due to customs clearance.
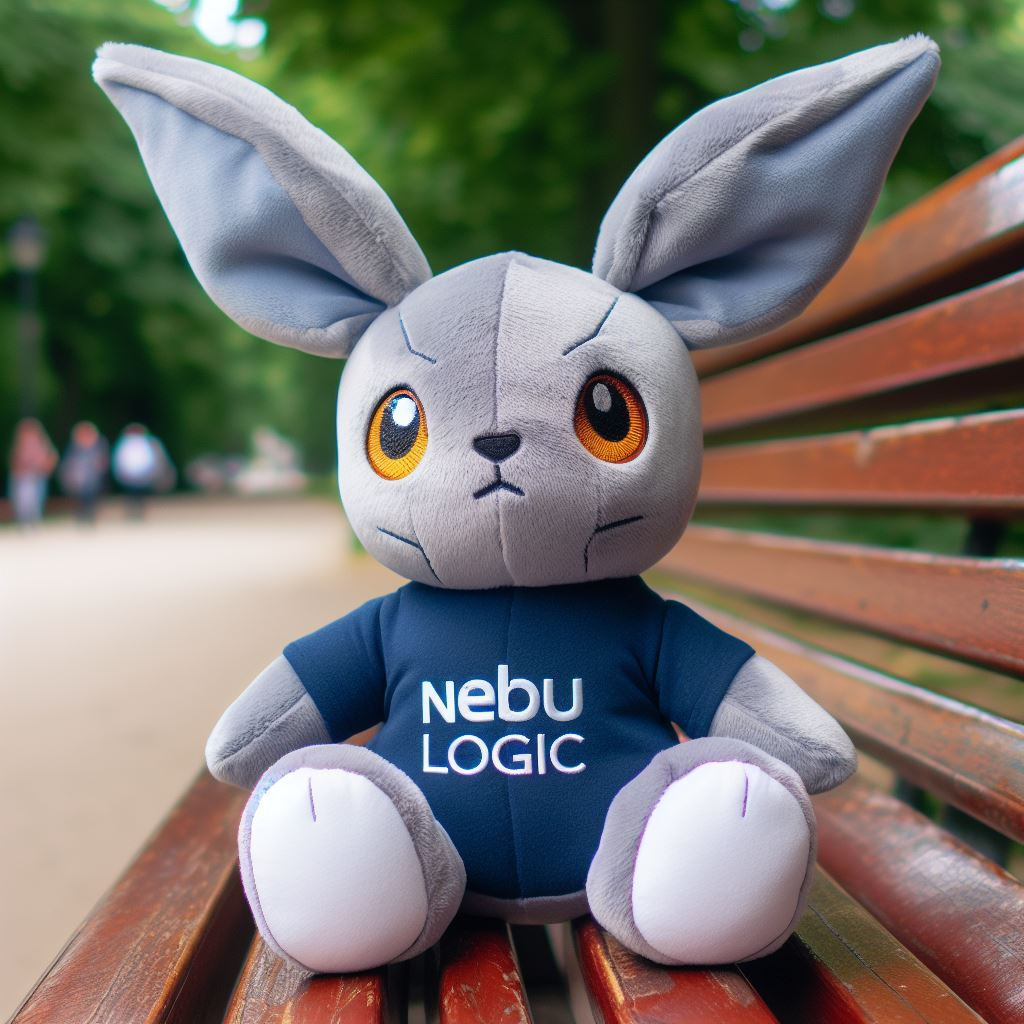
Sweet Reward of Patience: Benefits of Quality Production
Don't be discouraged by the wait for your custom plush! This section highlights the hidden advantages of quality production:
A Multi-Layered Scrutiny:
Unlike mass production where speed reigns supreme, custom plush creation allows for a more measured approach. Quality control checks are integrated throughout the process, acting like a safety net to catch any potential issues early on. Here's a breakdown of these checkpoints:
- Pre-Production Checks:
- Material Scrutiny: Fabrics and stuffing materials undergo rigorous inspection to ensure they meet safety standards and are free of defects like tears, inconsistencies, or non-compliance with regulations.
- Pattern Verification: The production team double-checks the patterns against your approved design specifications. This meticulous attention to detail ensures the final plush matches your vision in size, proportions, and seam allowances.
- In-Line Checks:
- Sewing with Scrutiny: Throughout the sewing process, vigilant inspectors ensure seams are secure and utilize the correct stitch type specified in the design. No wonky seams or loose threads slip through the cracks here!
- Stuffing Symmetry: Trained personnel closely monitor the amount of stuffing used to guarantee the desired level of squishiness and proper shape retention. A custom plush that's too limp or unevenly filled is quickly identified and rectified.
- Embroidery Expertise: Every detail embroidered onto your custom plush, from facial features to logos, is meticulously inspected for accuracy and adherence to the design. No stray stitches or mismatched colors make it past this checkpoint.
- Final Inspection:
- Flaw Elimination: The finished custom plush undergoes a rigorous final inspection for any flaws, including:
- Missed stitches or loose seams
- Uneven stuffing distribution
- Misaligned or missing embroidery details
- Inconsistent color tones or fabric discrepancies
- Presence of all required safety features (e.g., flame retardant labels)
Beyond Visual Inspection:
Random samples might undergo additional safety testing in independent labs for markets or age groups (especially for children's toys). It can include flammability testing, chemical content analysis, and small parts testing for choking hazards.
The Benefits of Meticulousness:
- Safety First: Stringent quality control checks prioritize safety, especially for children. Ensuring materials meet safety standards and there are no choking hazards or loose parts is paramount.
- A Flawlessly Crafted Companion: Quality control checks guarantee a well-constructed custom plush with neat and secure stitching, even stuffing distribution, and a flawless finish. It translates into a more durable and visually appealing product that you can cuddle with confidence.
- Your Vision, Realized: By meticulously checking every detail, quality control ensures the final custom plush accurately reflects your design and meets your specific requirements. No unpleasant surprises here – you get the cuddly companion you envisioned!
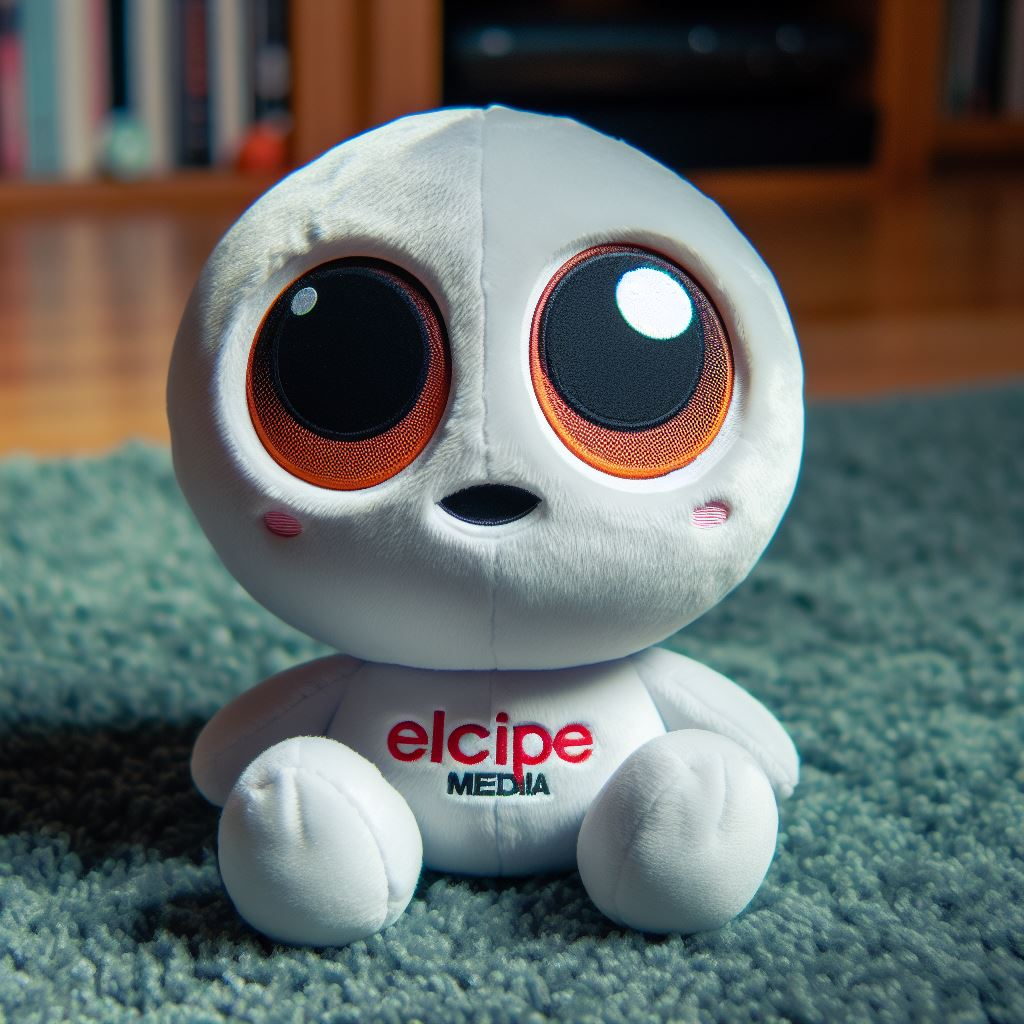
Planning for Perfection: Shorten Your Wait for Your Custom Plush
Eager to cuddle your custom plush creation but impatient for its arrival? This section equips you with valuable tips to optimize your wait time:
- Communicate Your Needs: Discussing your desired timeline with the manufacturer upfront helps them manage expectations and potentially suggest ways to streamline production.
- Order Simplicity: Complex designs with intricate details or embroidery can extend the production time. Consider simplifying minor elements to potentially expedite the process without compromising your vision.
- Plan for the Future: Ordering larger quantities upfront can be more cost-effective in the long run, especially for promotional purposes. It can save you time on future orders.
- Material Matters: Readily available fabrics and common stuffing materials typically translate to a faster turnaround than unique or specialty materials that require sourcing.
- Be Order-Ready: Having your design finalized and any approvals completed before placing your order allows the manufacturer to begin production sooner.
- Communicate and Collaborate: Open communication with the manufacturer throughout the process helps them to address any questions or concerns and potentially identify opportunities to optimize the timeline.

Optimizing Your Wait Time for Custom Plushie Creation: A Guide to Efficiency
The wait for a custom plush toy can be agonizing, but the anticipation is all the sweeter because you'll receive a one-of-a-kind cuddly companion. This section delves into strategies you can employ to streamline the production process and shorten your waiting time:
- Finalize Your Design Early: Embrace Clarity from the Start
- Clear Communication, and Efficient Production: The initial stage sets the foundation for a smooth production process. By finalizing your design early and providing the manufacturer with proper specifications, you eliminate potential delays caused by design revisions or misunderstandings.
- Complete Artwork for Seamless Integration: Having finalized artwork, including sketches, color palettes, and embroidery details, allows the manufacturer to directly translate your vision into production patterns and avoid any ambiguity.
- Order in Advance: Planning for the Perfect Present
- Predictability for Production Scheduling: Knowing your desired delivery date well in advance allows the manufacturer to schedule your custom plush production efficiently within their existing workload. This proactive approach helps avoid last-minute scrambling and potential delays.
- Seasonal Surges and Smart Strategies: If your custom plush is intended for a specific event or holiday season, placing your order well ahead of time is crucial. Manufacturers often experience higher demand during these periods, and early planning ensures your order gets incorporated into the production schedule without a lengthy wait.
- Communicate Clearly: Building a Bridge of Understanding
- Open Communication for a Smooth Journey: Maintaining open communication with the manufacturer fosters a collaborative environment. Don't hesitate to ask questions about materials, production timelines, or any concerns you might have.
- Proactive Problem-Solving: Clear communication allows the manufacturer to address potential issues early on and suggest alternative solutions if needed. This proactive approach can help prevent delays caused by misunderstandings or unexpected roadblocks.
- Consider Express Options (When Available): Speed at a Premium
- Expedited Production for Impatient Cuddlers: Some manufacturers might offer expedited production options for an additional fee. It can be a lifesaver if you have a pressing deadline or can't wait to get your hands on your custom plushie creation.
- Understanding the Trade-Off: While express options shorten the waiting time, they typically come at an additional cost. Weigh the urgency of receiving your custom plush against the budget you've allocated for the project.

EverLighten: Where Quality Meets Speed in Custom Plush Creation
EverLighten goes beyond simply creating custom plush toys; they strive to deliver high-quality products in the fastest time possible, prioritizing client satisfaction throughout the process. Here's how EverLighten exemplifies this commitment, as evidenced by the projects for McLennan Community College and Yellowpike Media:
McLennan Community College's Highlander Mascot:
- Challenge Accepted: EverLighten embraced the challenge of creating a complex design with various materials and accessories within a tight timeframe. Their dedication to client needs shines through by accepting the project despite the complexity.
- Communication is Key: Deep communication with the college ensured a clear understanding of their vision for the mascot custom plush. This collaborative approach minimized revisions and delays.
- Going the Extra Mile: EverLighten sourced the specific fabric required for the mascot's attire, demonstrating their commitment to detail and client satisfaction.
- Revisions for Perfection: EverLighten readily incorporated client feedback, making multiple revisions to the sword, clothing, and accessories until the college was completely satisfied.
Yellow Pike Media's Custom Plushie Gifts:
- Timely Delivery Despite Complexity: EverLighten delivered the custom plush toys for Yellowpike Media in just 15 days, exceeding expectations for a typical 20-30 day turnaround, even with the unique sitting position and logo embroidery.
- Creative Problem-Solving: When Yellowpike Media became unavailable, EverLighten's team proactively pursued communication to obtain the necessary files and begin the project.
- Exceeding Expectations: EverLighten addressed Yellowpike Media's dissatisfaction with the initial prototype by creating multiple options with various sitting positions and sizes, ensuring the client received exactly what they envisioned.
EverLighten's Competitive Advantage:
These real-world examples showcase EverLighten's dedication to several principles:
- Client Focus: EverLighten prioritizes understanding and fulfilling client needs, even when faced with challenges.
- Communication and Collaboration: Open communication fosters a collaborative environment, minimizing revisions and delays.
- Resourcefulness and Problem-Solving: The EverLighten team demonstrates resourcefulness in sourcing materials and problem-solving skills in addressing client concerns.
- Speed without Compromising Quality: EverLighten prioritizes efficient production processes without sacrificing quality or craftsmanship.
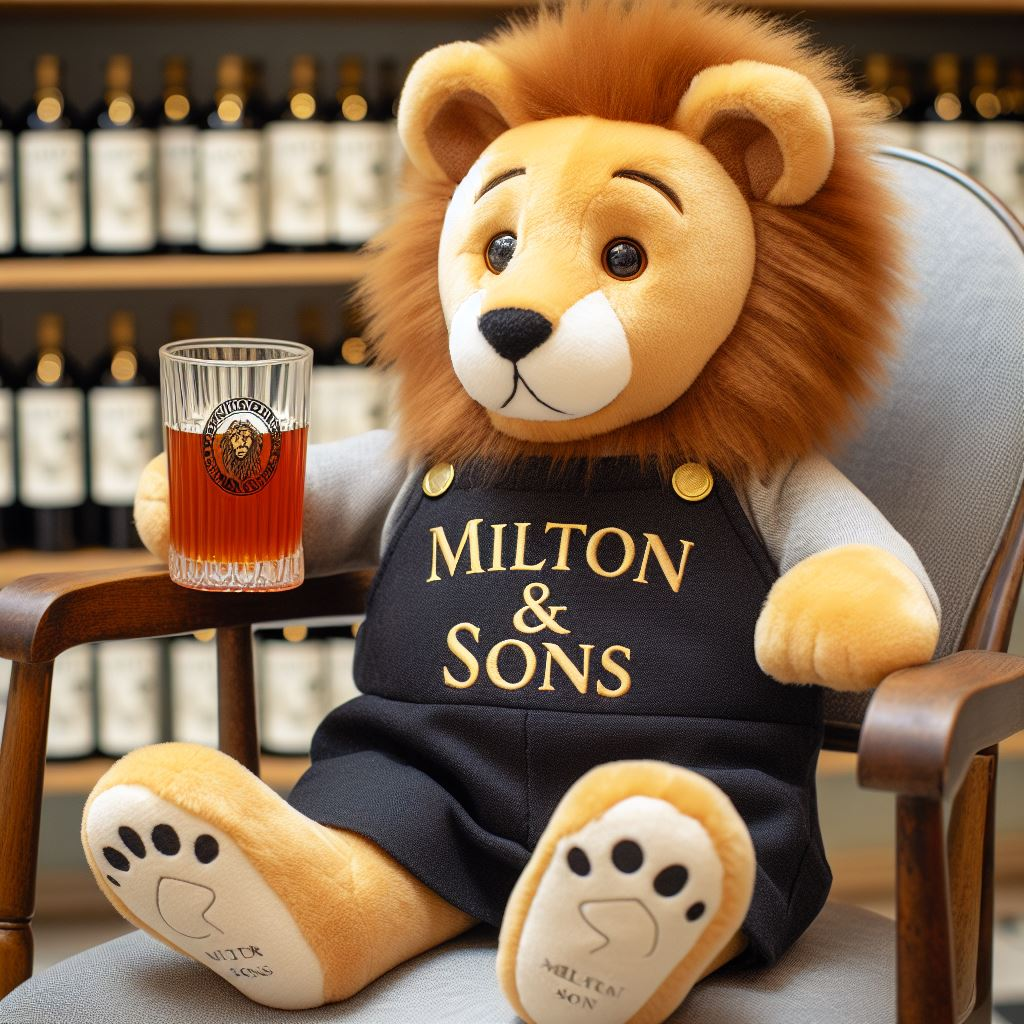
Bring Your Custom Plushie Dreams to Life: Experience the EverLighten Difference
EverLighten isn't just about creating custom plush toys; it's about transforming your vision into a cuddly companion that embodies your unique spirit. We take pride in exceeding expectations, as demonstrated by the stories of McLennan Community College and Yellowpike Media.
Here's what sets EverLighten apart:
- 100% Customization: Design your dream custom plush from scratch, or personalize an existing one. The possibilities are endless!
- 100% Quality Check: Every custom plush undergoes meticulous inspection to ensure it meets the highest safety standards and flawless craftsmanship.
- Free Design Help: Our expert design team is here to collaborate and refine your ideas into a perfect custom plush.
- Worldwide Delivery: We deliver your cuddly creations directly to your doorstep, no matter your location.
- 24/7 Support: Our dedicated team is always available to answer your questions and guide you through the process.
- Unlimited Revisions: We'll work tirelessly with you until you're completely satisfied with your Custom plush design.
- Low MOQ: Whether you need a single Custom plush or a larger quantity, we cater to your needs.
Ready to bring your Custom Plushie dream to life?
Visit our website today or contact our friendly team to discuss your project. We're passionate about creating high-quality, custom plushie toys that spark joy and connection. Let EverLighten be your partner in turning your vision into a cuddly reality!
FAQs:
- How long does it take to receive a custom push toy?
The wait time for your custom plush can vary depending on several factors, including
- The complexity of Design: A simple design with readily available materials will typically have a faster turnaround compared to a complex design with intricate details or embroidery.
- Order Quantity: Larger orders might require additional production scheduling adjustments and could take slightly longer than a single custom plush creation.
- Material Availability: If your design requires unique or specialty materials that need to be sourced, it might extend the wait time slightly.
General timelines can range from:
- 2-4 weeks: For simpler designs with readily available materials and a single custom plush order.
- 4-8 weeks: For moderately complex designs or small bulk orders.
- 8+ weeks: For highly complex designs, large bulk orders, or designs requiring unique materials.
- Can I expedite the production of my custom plush toy?
Some manufacturers, like EverLighten (as mentioned in the blog!), might offer expedited production options for an additional fee. It can be a great option if you have a pressing deadline.
- How can I shorten my wait time for a custom plush?
Here are some tips to potentially optimize your wait time:
- Finalize your design early: The sooner the manufacturer has your final design, the sooner they can begin production.
- Order in advance: Planning, especially for seasonal needs, allows the manufacturer to incorporate your order efficiently into their production schedule.
- Communicate clearly: Maintaining open communication with the manufacturer allows for early identification of potential issues and smoother problem-solving.
- Consider readily available materials: Choosing common fabrics and stuffing materials might lead to a faster turnaround than unique specialty materials.
- What can I do while I wait for my custom plush?
The wait can be exciting! Here are some ideas:
- Track your order: Many manufacturers provide tracking information so you can follow your custom plush's journey.
- Prepare a special welcome: Consider where you'll display your custom plush or plan a fun unveiling for a gift recipient.
- Dream about the possibilities: Custom plush toys are a great way to express creativity. Think about future custom plushie designs you might create!