Mitigate Risks Associated with AI Adoption in Small Garment Factories and Brands
| Oct, 29 , 24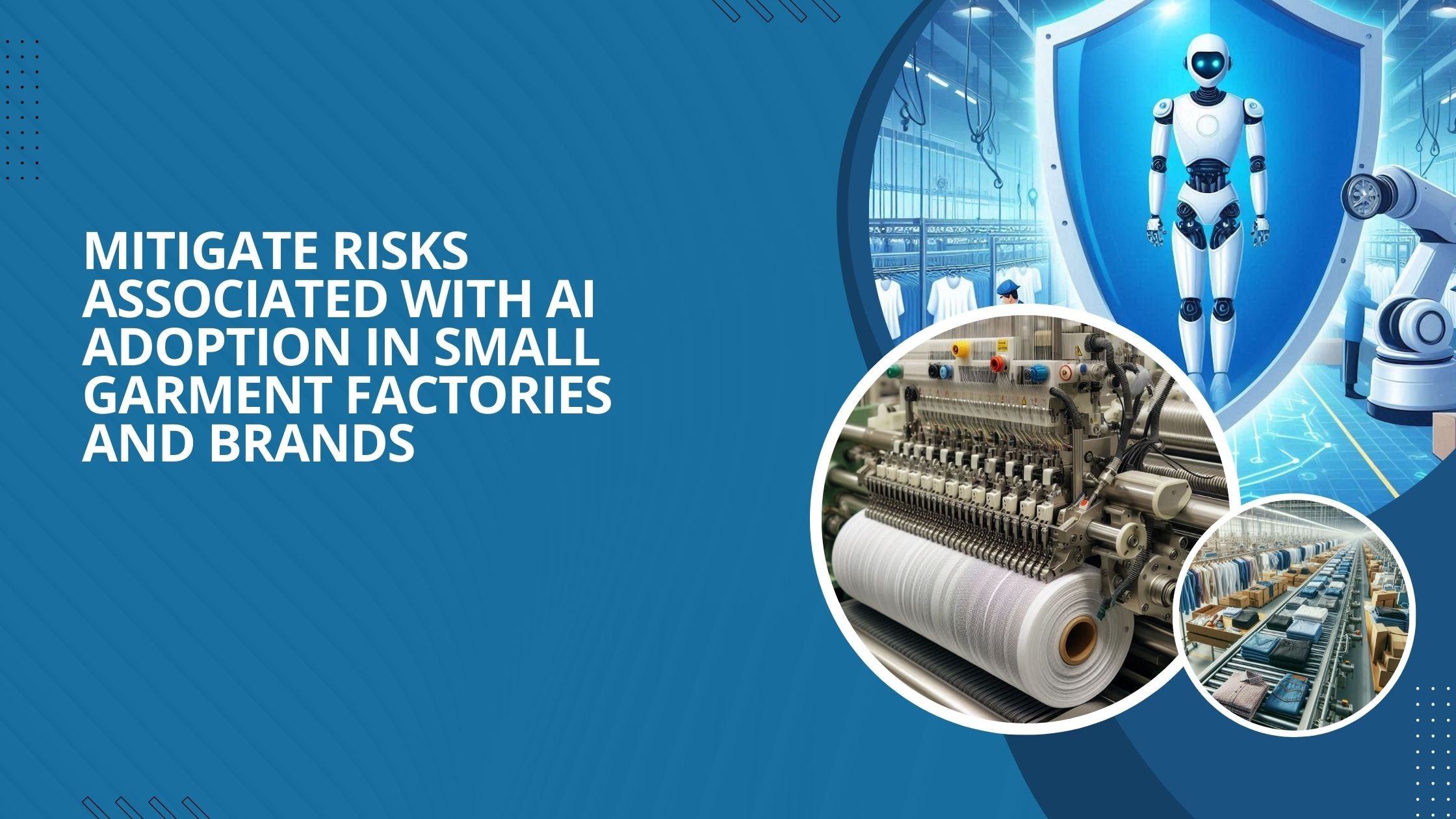
Is your small garment factory or brand ready to leap into AI but worried about potential risks? As artificial intelligence becomes an increasingly essential part of the manufacturing landscape, small garment factories and brands are eager to take advantage of its benefits—such as improved efficiency, better quality control, and enhanced customer personalization. Despite its potential benefits, AI adoption faces certain challenges. While AI adoption offers significant advantages, it also comes with risks that small garment factories and brands need to mitigate for successful implementation.
We will explore the common risks associated with AI adoption in small garment factories and brands and provide actionable strategies to mitigate them effectively. From data privacy concerns to high initial investment and technical challenges, we will learn how to navigate these issues and successfully integrate AI into your operations. Here are a few significant stats:
- Data Privacy and Security: A study by PwC found that 83% of companies are concerned about data privacy and security risks associated with AI adoption.
- Initial Investment: The upfront costs of implementing AI systems can be significant, with estimates ranging from $500,000 to $1 million for small to medium-sized businesses.
- Technical Challenges: A study by Accenture revealed that 43% of organizations cited technical challenges as a significant barrier to AI adoption.
We will guide you through strategies to manage these challenges and ensure a smooth transition into AI-enhanced operations for your business. First, let us understand a few risks of AI adoption in small garment factories.

Common Risks of AI Adoption in Small Garment Factories
- Technological Infrastructure Risks
Small garment factories often rely on legacy systems and machinery that may not be compatible with modern AI technology. The challenge lies in integrating AI-driven tools into existing operations, especially when the technological infrastructure is outdated.
- Challenges of Outdated Systems: Implementing AI in a factory with old equipment can lead to technical difficulties, resulting in system inefficiencies or breakdowns. Outdated machinery may require significant upgrades or replacements before integrating AI.
- Compatibility Issues: AI systems often require seamless data flow and connectivity between various departments, which can be challenging with older technologies that do not support advanced data sharing or automation.
- Workforce Skill Gap
AI implementation often requires new technical skills, such as operating AI-powered machines, managing AI systems, and interpreting data insights. The risk arises when employees are not adequately trained or lack the required technical skills to work with these new systems.
- Skill Deficiencies: Many workers in small garment factories are skilled in manual processes but may struggle with the technical demands of AI systems, from data analysis to operating automated machines.
- Training Gaps: It can slow down production and diminish the potential benefits of AI adoption if workers are untrained.
- High Initial Costs
AI adoption requires a significant financial investment, particularly for small garment factories with limited capital. The upfront costs include AI software, hardware, system integration, and potential upgrading infrastructure and employee training.
- Capital Investment: The cost of acquiring AI technology can range from $500,000 to $1 million for small to medium-sized businesses, according to Forbes. It can be a daunting expense, especially if the factory does not have immediate cash flow to support the investment.
- Cost Overruns: Poor planning or unexpected complications during implementation can lead to cost overruns, putting a financial strain on the business.
- Data Privacy and Security Risks
AI systems utilize and process extensive data. It has implications for data privacy and security. Protecting sensitive customer and production data when integrating AI solutions is essential to prevent breaches or compliance violations.
- Data Protection Concerns: AI systems often require access to customer information, production schedules, and inventory data, all of which can be vulnerable to hacking or misuse if not secured.
- Compliance Risks: Depending on the country or region, there may be strict data protection regulations that factories must comply with, such as GDPR in Europe or CCPA in California.
- Operational Disruption
AI-based operations can lead to temporary disruptions as new systems are installed, tested, and integrated with existing workflows. These disruptions may impact production timelines, lead to downtime, and affect overall efficiency.
- Downtime Risks: Integrating AI into the workflow may require halting production temporarily, which can delay orders and affect customer relationships.
- Learning Curve: Employees may take time to adapt to the new AI-driven systems, further slowing down production during the initial phase.
- Resistance to Change
One of the most significant risks to AI adoption is the resistance from employees, especially those who fear that AI could replace their jobs or who struggle to understand the new technology. Resistance can slow down the adoption process and lead to internal conflicts.
- Fear of Job Loss: Workers may view AI as a job security threat, leading to reluctance or outright resistance to the new systems.
- Lack of Understanding: Without clear communication, employees may not understand the benefits of AI or how it can enhance their roles rather than replace them.

Benefits of Proactive Risk Mitigation in Small Garment Factories and Brands
- Reduced Downtime: Minimizing Operational Disruption by Careful Planning and Gradual Implementation
Proactive risk mitigation is essential for preventing costly operational disruptions during AI adoption. By carefully planning the implementation of AI technologies and taking a gradual approach, small garment factories can ensure a smooth transition with minimal downtime.
- Gradual Integration: When factories implement AI solutions in phases, starting with low-risk areas like inventory management or quality control, they can avoid large-scale interruptions in production. This approach allows for real-time adjustments, minimizing the impact on day-to-day operations.
- Testing and Monitoring: Checking AI systems during early-stage implementation can help factories identify potential issues before they escalate into disruptions. By addressing technical problems promptly, factories can maintain consistent production schedules and avoid delays.
- Preventing Employee Confusion: A phased approach helps employees adapt to new AI systems, reducing confusion and frustration. Proper training and incremental system rollouts allow workers to become familiar with the technology without overwhelming them.
Key Benefits: By reducing downtime, factories maintain production levels, avoid delays in meeting orders, and ensure smoother operations during the transition to AI-powered systems.
- Cost Savings: Saving Money by Avoiding Unforeseen Expenses Related to Poorly Executed AI Integration
Proactively mitigating risks associated with AI adoption leads to significant cost savings. Small garment factories and brands can avoid the high costs that often result from poorly executed AI integration, such as technical errors, operational delays, or the need for retraining.
- Preventing Rework and Delays: Poorly executed AI implementation can lead to production errors, defective products, or inefficient processes. All of which require costly rework or correction. Factories avoid these extra expenses by planning AI integration and checking systems.
- Avoiding Unnecessary Investments: Without a clear strategy, factories may invest in AI solutions that do not suit their specific needs or scale. Proactive risk mitigation helps factories select the right AI tools and avoid overspending on unnecessary or overly complex technology.
- Efficient Use of Resources: Proper planning ensures efficient use of resources (financial, human, or materials). It helps avoid hidden costs, such as overtime wages due to delays or penalties for late deliveries.
Key Benefits: Factories can manage their budgets more effectively, avoid costly mistakes, and ensure they get the best return on their AI investment.
- Competitive Advantage: Staying Ahead of Competitors by Adopting AI Efficiently and Improving Product Quality and Speed to Market
Proactive risk mitigation allows small garment factories and brands to adopt AI more efficiently, giving them a competitive edge. By integrating AI technologies smoothly and without disruptions, factories can enhance product quality, speed up production processes, and deliver to market faster.
- Enhanced Product Quality: AI systems can improve quality control processes by detecting defects and ensuring consistency in production. By minimizing errors early on, factories can produce higher-quality garments that meet or exceed customer expectations.
- Faster Time to Market: Factories adopting AI can optimize production schedules and reduce lead times. AI-driven automation and predictive analytics allow factories to streamline workflows, meet tight deadlines, and respond to market demands more quickly.
- Innovation and Customization: Proactive AI implementation enables factories to offer more innovative and customized products. AI tools can facilitate personalized designs, niche market offerings, and faster product iterations, helping brands stand out from competitors.
Key Benefits: By improving product quality and speeding up time to market, factories and brands can attract new customers, retain existing ones, and establish themselves as leaders in their respective markets.

Strategies to Mitigate Risks of AI Adoption in Small Garment Factories and Brands
- Start Small, Scale Gradually
One of the most effective strategies for mitigating risks associated with AI adoption is to begin with small, low-risk processes. This incremental approach allows factories and brands to test the capabilities of AI technology without disrupting overall operations.
- Focus on Low-Risk Processes: Small garment factories can start by applying AI to relatively simple and low-risk tasks, such as quality control or inventory management. These areas can benefit from automation and data-driven insights, providing a solid foundation for broader AI implementation.
- Pilot Programs: Launching pilot programs helps the business evaluate the effectiveness of AI tools and gain practical experience. Starting small enables factories to identify potential challenges and make adjustments before scaling AI across the entire operation.
Key Benefits: This gradual approach reduces the risk of operational disruptions, minimizes costs, and provides a controlled environment for testing AI applications.
- Employee Training and Upskilling
One of the most significant risks to successful AI adoption is the lack of technical skills. Investing in comprehensive training programs is essential for overcoming this challenge and ensuring employees can operate AI-driven systems effectively.
- Bridging the Skill Gap: AI technology often requires new skills such as machine operation, data interpretation, and an understanding of AI-driven systems. By offering targeted training and upskilling programs, factories can equip employees with the knowledge they need to adapt to new technologies.
- Continuous Learning: Beyond initial training, fostering a culture of continuous learning is crucial. AI technology evolves rapidly, and regular workshops or certifications can help employees stay up-to-date with the latest developments.
Key Benefits: Skilled employees are more confident and productive, allowing the factory to leverage the full potential of AI without risking delays or errors due to a lack of expertise.
- Cost Management Strategies
One of the primary concerns for small garment factories adopting AI is the high upfront investment. To mitigate this financial risk, factories should explore flexible cost management strategies.
- Leasing Options: Instead of purchasing expensive AI hardware outright, factories can explore leasing AI equipment. It reduces initial costs and allows factories to upgrade to newer technologies as they become available.
- Cloud-Based AI Tools: Cloud-based AI solutions offer a more affordable and scalable option for small factories. These tools eliminate the need for costly on-premise systems, and factories only pay for what they use.
- Working with Vendors: Collaborating with AI vendors to explore payment plans or software-as-a-service (SaaS) models can make AI adoption more affordable. Vendors often provide tailored packages that align with a factory’s budget and needs.
Key Benefits: These strategies reduce the financial burden of AI adoption, allowing factories to manage costs more effectively and invest gradually over time.
- Cybersecurity Best Practices
AI systems often handle vast amounts of sensitive data, including customer information and proprietary production details. Ensuring data privacy and protection from cybersecurity threats is critical to mitigating the risks associated with AI adoption.
- Data Encryption: Implement secure encryption methods to protect data in transit and storage. It secures sensitive information from unauthorized use.
- Regular Security Audits: Strengthen the security of the AI system by conducting regular security audits. Partnering with cybersecurity experts or AI vendors who prioritize security can help small garment factories avoid costly data breaches.
- Compliance with Regulations: Ensure the factory complies with relevant data protection regulations, such as GDPR, to avoid legal penalties and maintain customer trust.
Key Benefits: A robust cybersecurity framework reduces the risk of data breaches, protects the reputation, and ensures compliance with industry regulations.
- Collaborate with AI Experts
Partnering with AI experts or consultants is one of the best ways to ensure a smooth transition to AI-powered operations. Expert guidance can help factories navigate the complexities of AI adoption, avoid common pitfalls, and maximize the benefits of AI technology.
- AI Consultants: AI consultants can help small garment factories assess their current capabilities, choose the right AI solutions, and implement systems effectively. They provide industry-specific insights and strategies tailored to unique needs.
- Vendor Collaboration: Partnering with AI vendors specializing in the garment industry allows factories to receive customized solutions and support. Vendors often provide training and continuous support, ensuring complete optimization of AI systems for maximum efficiency.
Key Benefits: Collaboration with AI experts reduces the learning curve, ensures best practices, and increases the likelihood of successful AI implementation.
- Foster a Culture of Innovation
One of the biggest challenges in AI adoption is overcoming resistance to change, particularly from employees who fear AI will replace their jobs. By fostering a culture of innovation, small garment factories can encourage employees to see AI as a tool that enhances their roles rather than replacing them.
- Employee Involvement: Involve employees in the AI adoption process from the start. Motivate them to contribute ideas and provide feedback on how AI tools can improve their daily tasks. It helps to demystify AI and reduce fear.
- Focus on Augmentation: Emphasize that AI will augment human work, not replace it. AI can automate repetitive tasks, freeing employees to focus on higher-value activities such as problem-solving, creativity, and innovation.
Key Benefits: A positive attitude toward AI fosters collaboration, reduces resistance, and leads to a more innovative, forward-thinking workforce.

Unlock the Full Potential of AI for Your Garment Brand with EverLighten
Adopting AI can transform your small garment factory, improving efficiency, reducing costs, and giving you a competitive edge. However, mitigating the risks associated with AI adoption is vital to a successful transition. By starting small, training your workforce, and carefully planning the integration process, your factory can reap the many benefits of AI without disrupting operations.
At EverLighten, we understand the unique challenges of small garment brands. We are committed to helping your garment brand with cutting-edge solutions tailored to your specific needs. With 100% customization, 100% quality check, and design help, our services ensure your business stays ahead in a fast-changing market.
We can help you optimize your garment business. We offer worldwide delivery, 24/7 support, unlimited revisions, and low minimum order quantities (MOQs) to make your garments seamless and hassle-free.
Connect with EverLighten today and start your journey.
FAQs
- How can small garment factories afford the initial investment in AI?
Small garment factories can explore options like cloud-based AI tools, leasing AI solutions, or collaborating with vendors to reduce upfront costs. Additionally, starting with low-risk processes and scaling AI usage can help manage expenses.
- What training is needed for employees to adapt to AI systems?
Employees need both technical and soft skills training. Technical training covers machine operation, data analysis, and AI-driven tools, while soft skills focus on adaptability, problem-solving, and continuous learning.
- What are the AI applications suitable for small garment factories?
AI applications include quality control, inventory management, design automation, and predictive analytics for supply chain optimization. Factories can start by adopting AI to boost efficiency and reduce costs.
- How do I ensure data privacy when integrating AI systems?
Implement robust cybersecurity protocols, including encryption, secure access controls, and regular audits. Work with AI vendors that prioritize data security and ensure compliance with relevant data privacy regulations.
- How can I overcome employee resistance to AI adoption?
Fostering a culture of innovation, offering comprehensive training, and demonstrating how AI can enhance roles rather than replace jobs can help ease employee concerns.