20 Tips For Building A Collaborative Human and AI Work Culture in Small Garment Factories and Brands
| Jul, 23 , 25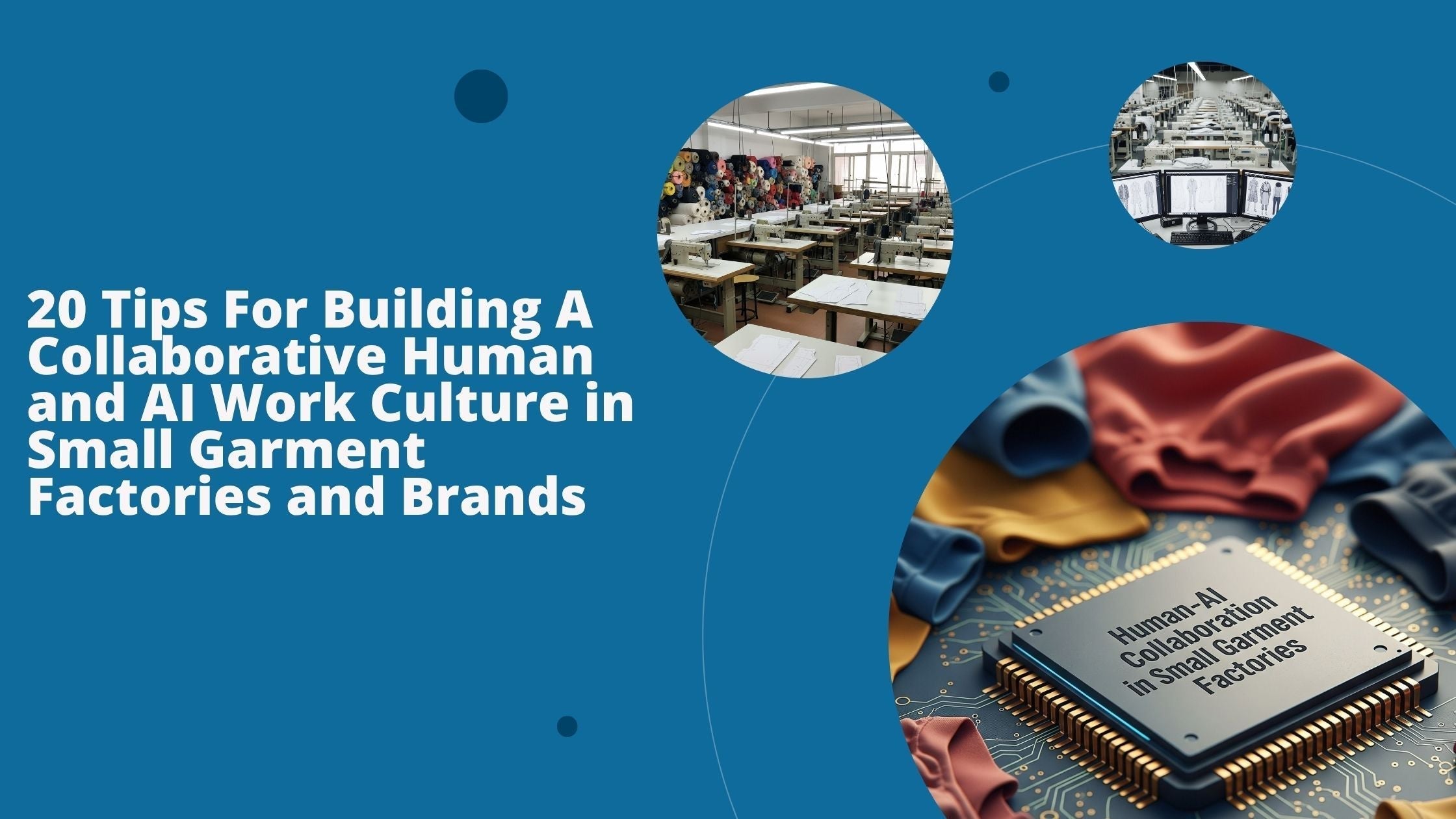
The hum of sewing machines and the skilled hands of artisans have long defined the garment manufacturing industry. But a new era is dawning for small garment factories and brands – one where smart, AI-augmented production is a tangible reality. This transformation isn't about replacing the invaluable expertise of your workforce; it's about forging a powerful partnership. Imagine a collaboration where human ingenuity and the analytical prowess of Artificial Intelligence work hand in hand to elevate efficiency, ensure unparalleled quality, and even boost team morale within your small garment factory. By strategically blending the dexterity of your skilled labor with intelligent AI tools, your small garment brand can reach new heights in performance and innovation. Let's explore 20 practical tips to cultivate a thriving, collaborative human-AI work culture within your small garment factory and brand and reap the benefits of this powerful partnership.
Laying the Foundation for Collaboration
Embarking on an AI journey in your small garment factory requires a solid groundwork built on understanding and clear communication. It's not just about installing new tech; it's about preparing your team for a new way of working. The potential benefits of AI adoption include improved efficiency, enhanced quality control, and increased productivity.
1. Educate Your Workforce on AI Basics
Empower your workforce by demystifying AI. Many workers in small garment factories might worry that AI will take their jobs. Counter this by offering simple, hands-on training sessions that explain AI in practical terms, demonstrating how it can assist, rather than replace. Use examples relevant to their daily tasks, such as how AI can help identify fabric defects more quickly or suggest optimal cutting layouts. When your team understands the basics, they feel more in control and less apprehensive about the changes AI brings, realizing that AI is not a threat but a tool that empowers them.

2. Identify Manual Pain Points in Manufacturing
The best way to introduce AI is to have it solve real problems your team faces. Engage your operators directly. They're on the front lines and are familiar with the most tedious, repetitive, or error-prone aspects of their jobs. Is it constantly re-checking seams for inconsistencies? Struggling with precise pattern alignment on tricky fabrics? Use their feedback to pinpoint specific areas ripe for AI augmentation or automation. This approach ensures AI solutions are genuinely helpful and well-received within your small garment factory.
3. Set Realistic Goals for AI Adoption
For small garment brands and factories, a phased approach is crucial. By starting with high-impact areas where AI can deliver clear, measurable benefits, such as defect detection using computer vision or pattern matching, you can build confidence and demonstrate AI's value without overwhelming your team or resources. Other high-impact areas include inventory management, predictive maintenance, and production planning.

4. Communicate the 'Why' of AI to Teams
Transparency is key to buy-in. Clearly explain why your small garment factory is adopting AI. Emphasize that AI tools are there to support workers, making their jobs easier, more efficient, and often more interesting, rather than eliminating positions. Show how AI can act as a powerful assistant, particularly in areas like quality control, where it can spot minute flaws humans might miss due to its ability to process large volumes of data and identify patterns, or in production planning, where it can optimize schedules.
5. Appoint Human-AI Champions
Designate a 'bridge team' within your small garment factory composed of tech-savvy workers and supervisors. These individuals will be your Human-AI Champions. They'll act as internal experts, helping peers understand new tools, collecting feedback, and demonstrating best practices. Their role is crucial for monitoring the effective collaboration between humans and AI, troubleshooting minor issues, and helping to scale successful AI integrations across different departments. By having these champions in place, you can ensure that the transition to AI is as smooth as possible, with dedicated support for all team members and a clear path to successful AI adoption.

Human + AI on the Shop Floor
Once the foundation is laid, it's time to integrate AI directly into the daily operations of your small garment factory. The goal here is seamless collaboration, where AI acts as an intelligent assistant, enhancing human capabilities. This emphasis on the role of AI in enhancing human capabilities makes your audience feel more valued and integral to the process, rather than feeling overshadowed by technology.
6. Integrate AI with Sewing Stations Smartly
Think of AI at sewing stations as an extra pair of expert eyes. Instead of intrusive micromanagement, use real-time guidance systems that aid operators. It could involve visual cues projected onto fabric for perfect seam allowances or audio alerts for potential issues. The AI should serve as a helpful co-pilot, improving precision and consistency, rather than a system that dictates every move and potentially frustrates skilled workers in your small garment factory.
7. Train Staff to Work with Computer Vision Systems
Computer vision is a game-changer for quality control. Train your staff, especially quality checkers, on how to interpret AI alerts from these systems for defects, stitch inconsistencies, or fabric flaws. It's not enough for the AI to detect issues; your team needs to understand what the AI is flagging and why, enabling them to make informed decisions and take corrective action efficiently. This upskilling is crucial for any small garment brand seeking to maintain consistent quality.

8. Use AI to Optimize Line Balancing—With Human Input
AI can analyze complex data to suggest optimal line balancing. This process involves distributing work evenly across sewing stations to minimize bottlenecks and maximize throughput in your small garment factory. However, real-world variables, like a sudden machine breakdown or a particularly intricate design, require human judgment. Blend AI analysis with supervisor intuition. Let the AI provide data-driven recommendations, but empower supervisors to make final adjustments based on their experience, ensuring smooth operations without overloading workers.
9. Make Feedback Loops Human-Friendly
AI systems learn from data, and human feedback is invaluable for that learning process. Design feedback mechanisms that are easy for operators to use. If an AI system makes a recommendation, allow operators to review and even override it, provided they give a reason. It not only improves the AI's accuracy over time but also empowers your workforce, showing them their expertise is valued and integral to the AI's success, making them feel more involved and essential in the AI integration process.

10. Combine Human Skill and AI in Pattern Placement
Fabric waste is a significant cost for small garment factories. AI can suggest highly optimized pattern layouts to minimize waste, taking into account fabric width and grain. However, for specialty fabrics with unique textures, patterns, or stretch, human cutters often possess an intuitive understanding that AI might miss. Use AI to suggest initial layouts, but let experienced cutters make final, nuanced adjustments to ensure the best yield and quality, blending efficiency with craftsmanship.

Training and Upskilling in the AI Era
The integration of AI isn't a one-time event; it's an ongoing evolution that requires continuous learning and adaptation from your workforce.
11. Provide Continuous Learning Paths
To remain competitive in your small garment factory, invest in ongoing education and training. Offer short, digestible training modules on new digital tools, smart sensors, and the basics of machine learning relevant to their roles. These shouldn't be lengthy, intimidating courses but rather practical sessions that build skills incrementally, empowering workers to interact with new technologies comfortably.
12. Build Cross-Functional AI Task Teams
Break down departmental silos. Create hybrid teams that include mechanics who understand the machinery, operators who are familiar with the production process, and tech support staff who can effectively manage the AI systems. These cross-functional teams can collaboratively troubleshoot issues, identify new opportunities for AI integration, and share knowledge, fostering a holistic understanding of AI's role across your small garment factory.

13. Involve Workers in AI Testing Phases
Nothing builds trust and ownership like direct involvement. When introducing new AI tools, test them on live production lines with active worker feedback to ensure optimal performance. Don't just implement solutions top-down. Solicit their input on usability, effectiveness, and any unexpected challenges. This iterative process provides the practical tools well-suited to your small garment brand's specific needs, making your team feel valued and heard.
14. Celebrate Human-AI Milestones Publicly
Recognize and celebrate the successes driven by human-AI collaboration. Track productivity increases, quality improvements, or waste reductions directly attributable to the new systems. Publicly acknowledge the teams and individuals who contribute to these wins. It reinforces the positive impact of AI, motivates continued engagement, and builds a culture of innovation and shared achievement within your small garment factory.

15. Invest in Soft Skills for Supervisors
As technology evolves, so too must leadership. Equip your supervisors with essential soft skills like change management, coaching, and digital communication. They'll need to guide their teams through transitions, address concerns, and effectively communicate the benefits and challenges of AI integration. Strong leadership is paramount to ensuring a smooth and successful AI adoption journey for your small garment brand.
Safety, Morale, and Long-Term Culture
Beyond immediate productivity gains, the long-term success of AI integration in your small garment factory hinges on fostering a positive, safe, and evolving work culture.
16. Ensure AI Systems Are Transparent and Explainable
Avoid "black box" AI models where decisions are made without explicit reasoning. For critical applications, such as quality control or production planning, ensure that your staff understands how predictions or recommendations are generated. If an AI flags a defect, the system should ideally provide context (e.g., "irregular stitching detected at X point"). This transparency fosters trust and enables human oversight and learning.

17. Use AI to Reduce Repetitive Stress Tasks, Not Speed Up Output
AI should be a tool for worker well-being, not just accelerated production. Prioritize automating tasks that are repetitive, physically demanding, or tedious. It could include automated fabric inspections, boring data entry, or component sorting. The goal is to free up your workers from monotonous tasks, allowing them to focus on more skilled, creative, and fulfilling aspects of garment manufacturing, rather than simply pressuring them to produce more. It improves worker morale in your small garment factory.
18. Create a Safe Environment for Feedback and Failure
Innovation cannot happen without trial and error. Establish a culture where teams feel safe to voice concerns about AI tools, report glitches, or even admit when a system isn't working as expected, without fear of blame or being seen as "anti-tech." Encourage constructive criticism and use it to refine AI implementations. This open feedback loop is essential for continuous improvement and successful AI adoption.

19. Reward Collaboration Over Output Alone
Rethink your Key Performance Indicators (KPIs) slightly. While output remains important, also recognize and reward teamwork, adaptability to new systems, and effective collaboration with AI tools. This shift in focus encourages a more holistic approach to performance, valuing the seamless integration of human and artificial intelligence, and fostering a truly collaborative spirit within your small garment brand.
20. Review and Evolve Your Human + AI Playbook Quarterly
The world of AI is constantly evolving, and so should your approach. Schedule regular reviews (e.g., quarterly) of your human and AI playbook. Assess what's working well, what challenges have emerged, and what new opportunities AI might offer. Gather input from both the human users and the technical performance of the AI. This continuous refinement ensures your small garment factory remains agile and continues to leverage AI effectively for long-term success.

Elevate Your Garment Brand with EverLighten's Manufacturing
Ready to differentiate your small garment factory or brand and embrace the future of the manufacturing industry? At EverLighten, we're committed to helping businesses like yours thrive. Experience the power of:
-
100% Customization: Bring your unique designs to life with precision and accuracy.
-
100% Quality Check: Every garment meets the highest standards.
-
Free Design Help: Our experts assist you from concept to creation.
-
Worldwide Delivery: Reach your customers wherever they are.
-
24*7 Support: We're always here to assist you.
-
Unlimited Revisions: We work until your vision is exactly as you envisioned it.
-
Low MOQ: Start small and scale with confidence.
Connect with EverLighten today and transform your garment manufacturing operations!
FAQs
Q1: Is AI suitable for small garment factories, or is it just for large corporations? A1: Absolutely! While large corporations have adopted AI, it's becoming increasingly accessible and beneficial for small garment factories and brands. AI tools are now more affordable and user-friendly, offering significant advantages in efficiency, quality, and differentiation without requiring massive investments.
Q2: Will AI replace my existing workforce in my small garment factory? A2: Our focus, and the philosophy behind these tips, is on human-AI collaboration, not replacement. AI is best utilized to automate repetitive tasks, provide insights, and augment human capabilities, enabling your skilled workers to focus on more complex, creative, and value-added aspects of garment manufacturing.
Q3: What's the easiest way for a small garment brand to start integrating AI? A3: Start by identifying a single "pain point" in your manufacturing process that's repetitive or prone to error, like fabric defect detection or precise pattern cutting. Implement an AI solution for that specific area, gather feedback, and learn from the experience before expanding to other places.
Q4: How can I ensure my staff accepts and adopts new AI technologies? A4: Education, transparent communication, and involving them in the process are key. Break down AI basics, explain why it's being implemented (to support them, not replace them), and allow them to provide feedback and be part of testing new tools. Appointing internal "AI Champions" also helps.
Q5: What kind of benefits can a small garment factory expect from AI integration? A5: You can expect benefits such as increased efficiency through optimized processes, improved product quality via AI-powered defect detection, reduced material waste from better pattern placement, faster design iteration, and potentially enhanced employee morale by offloading tedious tasks.